先说结论,极限压缩成本的最终是质量受损,但是很多人并没有说清楚无脑降本到底是怎么样一步步蚕食产品质量的。
我只拿制造过程举例,这是位于苏D某汽车软内饰件生产制造商,它的主要客户就是BYD、大众、继峰这些知名企业。
说实话,第一次看到这个车间我是震惊的,我惊叹就这种现场管理怎么能进入汽车的一、二级供应链的。直到我去了别的制造商,才发现这车间都算还好的了。
对于终端用户,最可悲的是,你说它产品有问题,它说你使用习惯不对。毕竟100个人有100种使用习惯,你没法标准化场景,更无法拿出证据是它的产品问题。这种在近几年新能源产业链已经是明面上的事了。
回归正题,整车厂降本,这些供应商常见的转嫁手段:
1.员工从正式工变为劳务工,降低用人成本。风险就是,这种小公司培训制度不健全,很多甚至不培训就上岗,技能不足产品的不良、报废就增多;
2.减少人员配置,一个人干原来2-3倍的工作,砍掉质检人员。同样的,小公司制度不健全,一砍就直接影响品质;
3.减少项目技术人员,一个人做几个人的工作,甚至用低价招聘水平不行的人。导致模具、工艺不合格,做出来全是不良;
4.之前不良需要返工的产品,直接发货。之前判定报废的产品,返工后发货。从上到下都睁一只眼闭一只眼;
5.好的产品与不良品按一定的比例掺着发货,到客户端全凭运气;
6.没有利润的产品,再找代工厂。模式就有点类似最初的工程转包,一二三手。转几次之后,最初的标准和要求早就抛之脑后;
7.因为整车厂对于供应商供不上货导致停线,是有处罚的,某迪是3000/min。有时候老板被逼急了就是宁愿发不良品,也不能不发货。
最后也是最魔幻的,因为好坏参半的发货,有时候还没有客诉。那进一步的偷工减料就在路上了

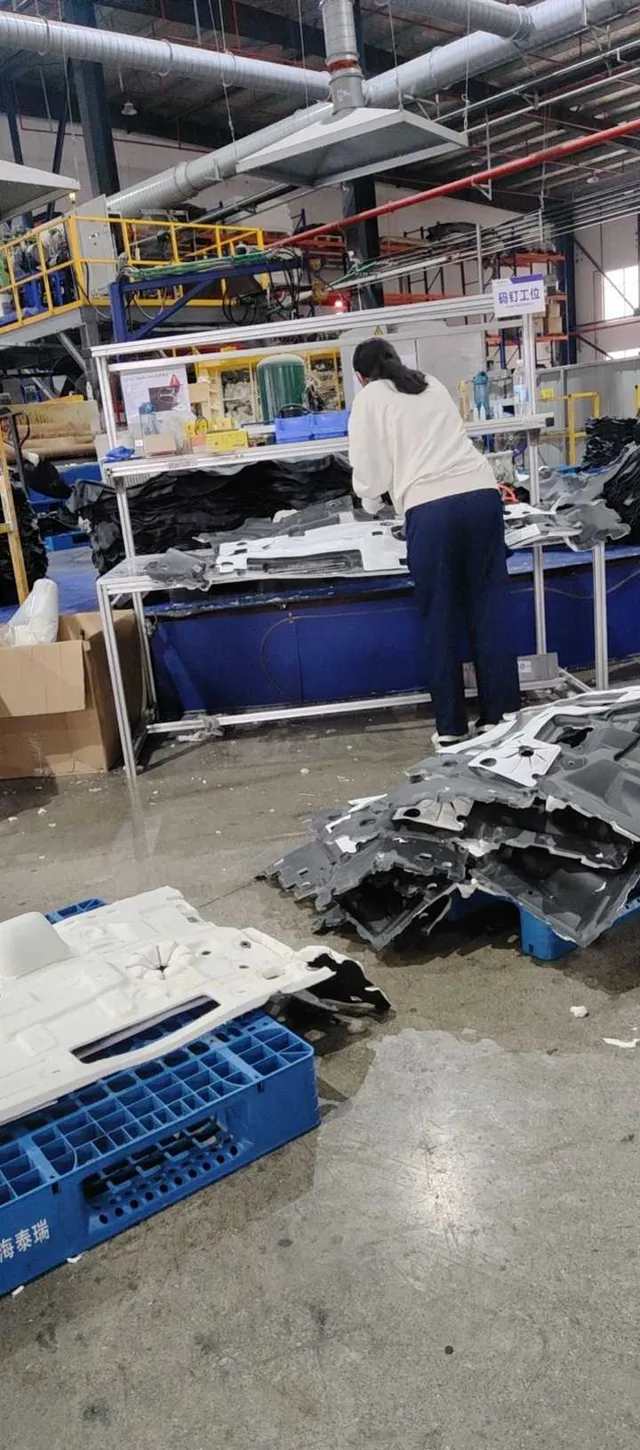
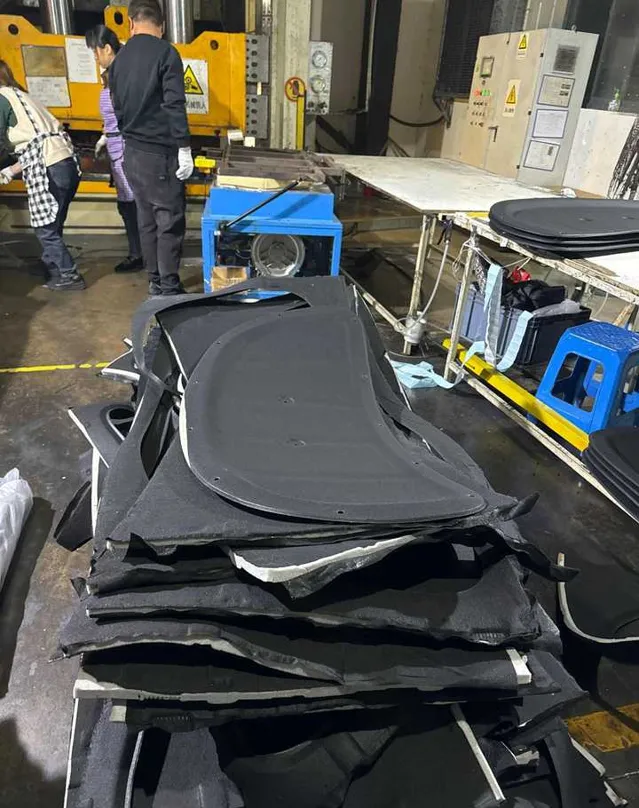
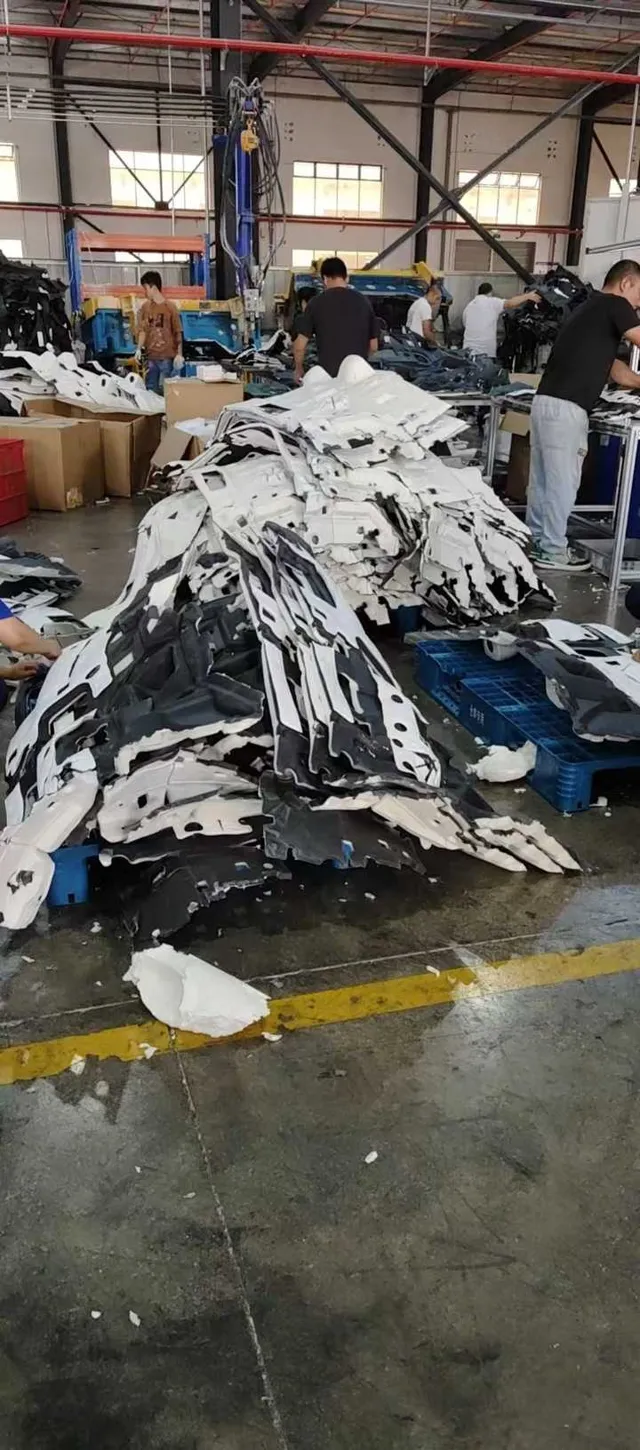