先說結論,極限壓縮成本的最終是質素受損,但是很多人並沒有說清楚無腦降本到底是怎麽樣一步步蠶食產品質素的。
我只拿制造過程舉例,這是位於蘇D某汽車軟內飾件生產制造商,它的主要客戶就是BYD、大眾、繼峰這些知名企業。
說實話,第一次看到這個車間我是震驚的,我驚嘆就這種現場管理怎麽能進入汽車的一、二級供應鏈的。直到我去了別的制造商,才發現這車間都算還好的了。
對於終端使用者,最可悲的是,你說它產品有問題,它說你使用習慣不對。畢竟100個人有100種使用習慣,你沒法標準化場景,更無法拿出證據是它的產品問題。這種在近幾年新能源產業鏈已經是明面上的事了。
回歸正題,整車廠降本,這些供應商常見的轉嫁手段:
1.員工從正式工變為勞務工,降低用人成本。風險就是,這種小公司培訓制度不健全,很多甚至不培訓就上崗,技能不足產品的不良、報廢就增多;
2.減少人員配置,一個人幹原來2-3倍的工作,砍掉質檢人員。同樣的,小公司制度不健全,一砍就直接影響品質;
3.減少專案技術人員,一個人做幾個人的工作,甚至用低價招聘水平不行的人。導致模具、工藝不合格,做出來全是不良;
4.之前不良需要返工的產品,直接發貨。之前判定報廢的產品,返工後發貨。從上到下都睜一只眼閉一只眼;
5.好的產品與不良品按一定的比例摻著發貨,到客戶端全憑運氣;
6.沒有利潤的產品,再找代工廠。模式就有點類似最初的工程轉包,一二三手。轉幾次之後,最初的標準和要求早就拋之腦後;
7.因為整車廠對於供應商供不上貨導致停線,是有處罰的,某迪是3000/min。有時候老板被逼急了就是寧願發不良品,也不能不發貨。
最後也是最魔幻的,因為好壞參半的發貨,有時候還沒有客訴。那進一步的偷工減料就在路上了

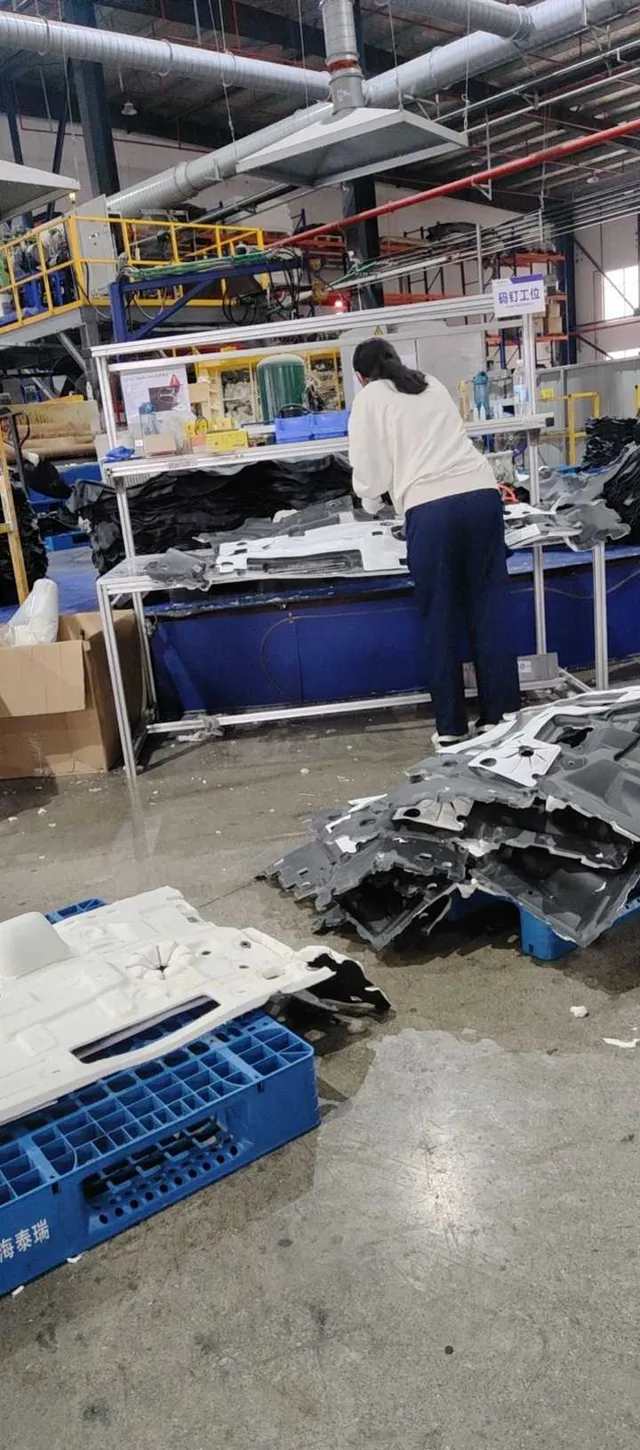
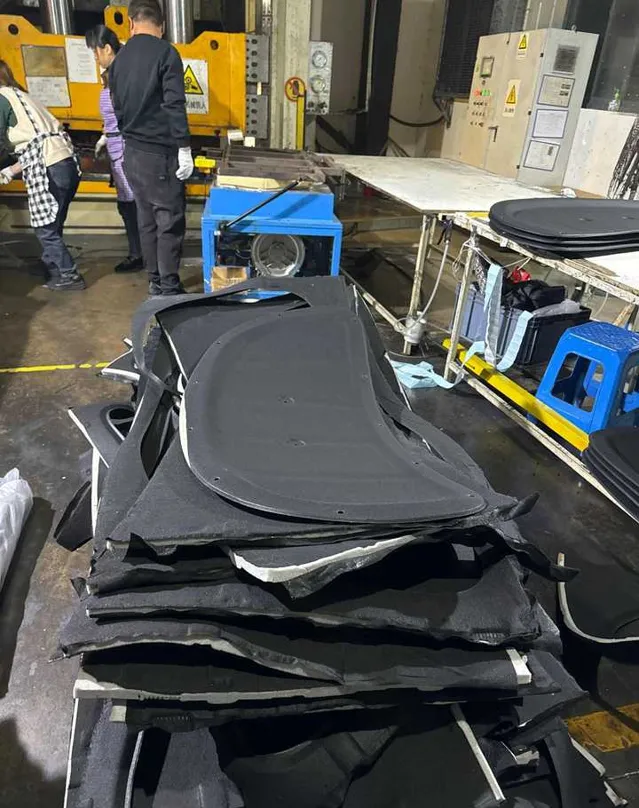
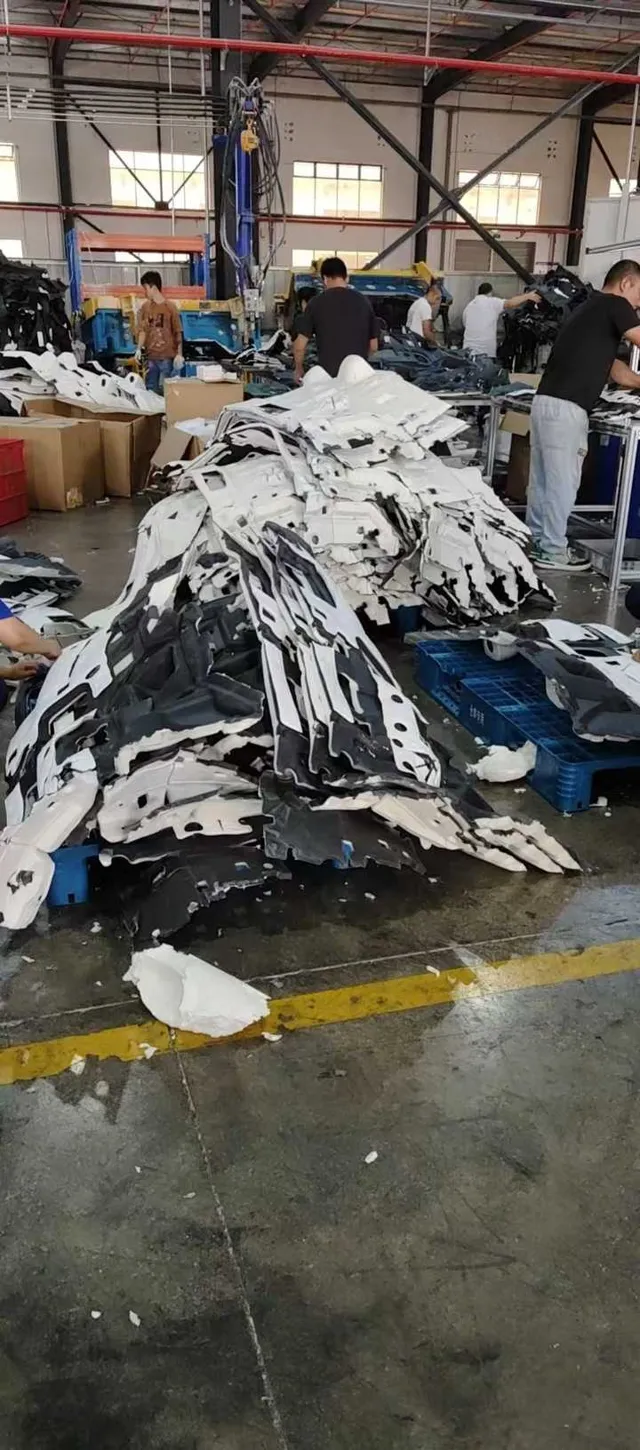