沒想到隨手寫的答案居然被編輯推薦了,很高興看到這麽多人對發動機相關的知識感興趣。先進航空發動機的設計和制造是一個非常復雜的系統工程,我只能盡力多給大家分享一些知識,也希望能有專業人士給大家做更好的科普。
航空發動機雖然會被人稱為工業皇冠上的明珠,但是其本身並沒有什麽神奇的地方,也不存在不可逾越的障礙。美英發動機技術先進首先是因為起步早,還在二戰之後的幾十年裏持續投入海量的資源,有著一流的人才長期耕耘,經歷過無數的失敗,才創造出這樣的工業奇跡,為人類翺翔藍天插上了強壯的翅膀。
因此,我們現階段在航發領域的落後是非常正常的,如果僅靠國家微薄的投入(相比美英)和短時間的積累,就在航發領域能比肩美英,甚至超越,反而是違反工程常識的。工程實踐是沒有捷徑可言的,必須紮紮實實的一步一個腳印走下去。人家之前做過的預研,走過的彎路,栽過的跟頭都是寶貴經驗,如果我們花費足夠的時間和精力,不吃幾次虧,是不可能達到相同的水平。國家也只是近幾年才開始大幅提升對航發領域的關註和投資,這也僅僅是補課而已。從這種角度看,我們國家現在的航發水平其實已經值得欣慰了。
互聯網、金融是社會經濟發展的能力倍增器,但是制造業才是根本。現在靠宣傳奉獻精神去吸引人才是很荒唐的,希望航發等高端制造業領域從業人員的薪資水平能體現這些產業的重要程度,吸引更多的人進入相關行業。這種高端制造業需要大量人力物力去維持,一旦落後就很追上先進水平了。
=====================================================================
0316增加一部份內容
=====================================================================
航空發動機是一個極端復雜的系統 ,我接觸過一些關於先進航發渦輪葉片的知識, 只就這一小部份內容跟大家分享一下 ,有什麽不對的歡迎探討。放張GP7000的圖,顯示一下系統的復雜程度(2170*1620應該可以點開看細節)。
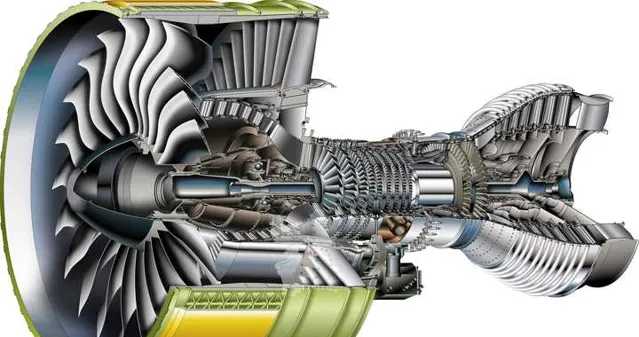
就我個人來看,我認為航空發動機是研發制造難度最大最頂級的現代工業造物。因為追求的是發動機在極為有限的空間內和極端惡劣條件下(高溫高壓高應力)保證長期的、穩定的、極端的效能。 衡量人類文明水平的一個標誌就是利用能量的水平,航發在極為有限的空間內實作了較高水平能量的穩定釋放(燃氣燃燒)和轉化(推動渦輪扇葉等旋轉,產生推力)。
如很多答主所說,航發上用的東西,一方面要求 優異的效能 ,一方面還要保證 長時使用的 穩定性和安全性 。火箭、飛彈上的部件也是在極端條件下使用,但是往往只需要保證能用幾百秒就可以了。而民航采用的先進航發往往要使用上萬小時(雖然有翻修過程),在整個過程中不僅不能發生任何問題,還要保證效能穩定。否則,可能造成幾百人罹難的慘劇。這幾方面的要求就把先進航發的設計研發制造門檻提高到地球上僅幾個國家能生產的地步。
別的領域不是很懂行,就大概介紹一下航發的原理、結構,主要說一些材料方面的吧。航發為了提高效能和減重,裏面有大量的空心結構,設計和加工非常困難。
現在的航空發動機有離心式和軸流式,現在主要都是軸流式,所以我就只介紹這部份。在空客、波音上面安裝的是渦輪扇葉(渦扇)式發動機。它的原理並不復雜: 空氣從最前面的風扇處入後,分為兩路,一路直接從外涵道排出,產生推力,一路進入壓氣機 (兩路空氣流量之比被稱為涵道比) ;經多級壓氣機風扇的壓縮,產生部份推力,瓦斯體積減小,壓力升高,繼續流入燃燒室; 燃燒室內點燃燃油和壓縮空氣的混合物,瓦斯加熱膨脹做功(產生推力),推動渦輪旋轉(產生阻力); 渦輪透過轉軸帶動風扇和壓氣機轉動,繼續吸入並壓縮空氣;燃氣推動渦輪旋轉之後排出,產生部份推力。

渦輪和壓氣機以及風扇是連在一或兩根同心軸上的(RR搞過3根同心軸套一起,感謝評論中@GRIT朋友的提醒),高 / 中 / 低壓渦輪分別帶動高壓壓氣機 / 低壓氣機 / 風扇轉動,燃燒室後面多級渦輪就像濾網一樣,把燃氣中的能量「濾」下來轉化成推力。下圖為典型的三轉子發動機示意圖。這樣的設計結構復雜,但是可以使風扇、低壓壓氣機和高壓壓氣機都執行中最理想的轉速上,提高效率和效能。高壓壓氣機,燃燒室和渦輪一般被稱為發動機的核心機。
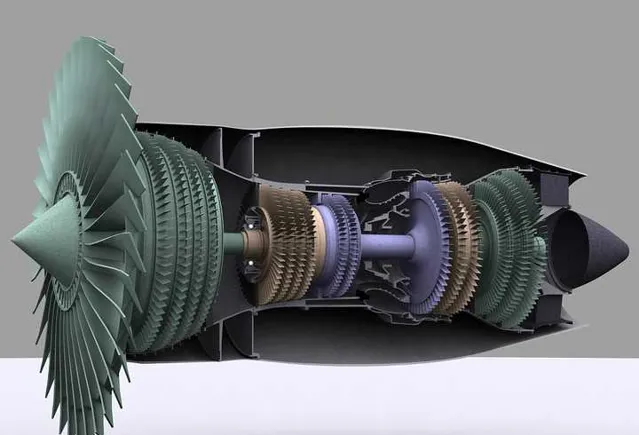
(google image找了一張新的圖片,更容易理解。
這是典型的3轉子發動機。顏色相同的部份是透過軸連在一起的。後面的紫色的是高壓渦輪,往後依次是中壓和低壓渦輪)
先從最前面開始,簡單講講風扇部份:
馬赫數較低的階段,渦扇發動機效率高,見下圖。常見的民航發動機都是大涵道比發動機,主要由風扇提供推力,燃油效率較高。 可以簡單的這麽認為:涵道比越大,風扇提供的推力比例越大,發動機的推力越大,也越省油(大家可以看到現在發動機直徑越來越大,葉片越來越長。 美國C-17發動機PW2040涵道比是6,推力是18噸; 中國運20試飛配的D30發動機的涵道比2.42,推力12.5噸。。。)。
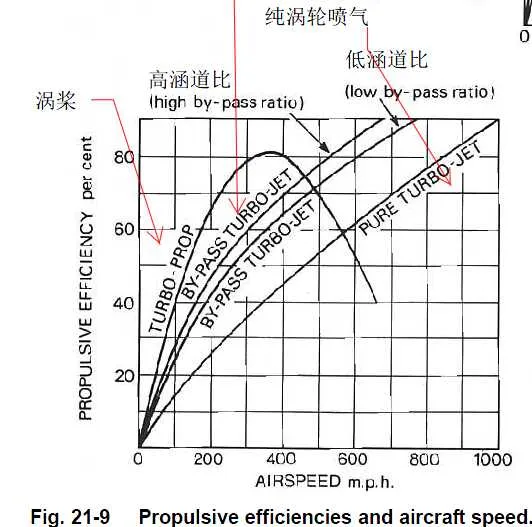
(Rolls-Royce)
早期的風扇是窄弦風扇,由實心鈦合金鍛造而成,為了提高風扇葉片的強度和抗振動效能,還在葉片上設計了凸肩,一圈葉片的凸肩組成一個加強環。放一個PW2000(跟PW2040一系列的)的圖,凸肩組成的加強環見箭頭處,現在大家坐飛機應該看不到這種發動機了吧。
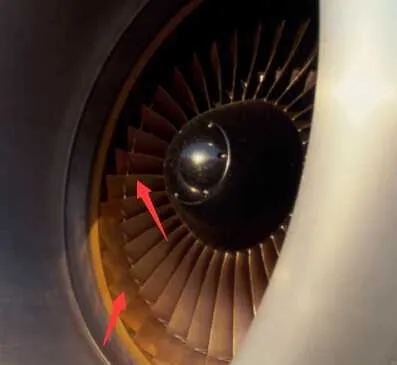
但是,實心葉片加凸肩的設計,降低了風扇的氣動效率低,葉片品質過大,這種葉片不適合更大推力發動機對風扇葉片的要求。現在采用的都是RR率先研發的 無 凸肩 寬弦空心風扇葉片 ,這種葉片是兩層鈦合金中間加上了一種蜂窩狀結構。采用這種設計,
風扇轉子葉片數量減少了1/3;轉子重量減輕了10%~30%;蜂窩芯結構還可改善葉片的減振特性;與帶阻尼凸肩的窄弦風扇葉片相比,葉柵通道面積加大,喘振裕度變寬,效率提高,壽命增加。RR公司在第一代寬弦葉片的基礎上,於1994年研究成功第二代寬弦空心風扇葉片。這種……風扇葉片芯部采用建築上所用的三角形桁架結構,取代了第一代寬弦風扇葉片的內部蜂窩芯板。這種三角形桁架結構不僅輕質,而且能承力,每片葉片重量比蜂窩芯葉片輕15%。該種葉片已經用於波音777和A330的Trent發動機上。該發動機風扇直徑為2.79m,葉尖速度為457m/s,每片寬弦葉片重量僅9kg!
引自 侯冠群, 尚波生. "寬弦風扇葉片技術的發展." 國際航空 12 (2002): 45-47.
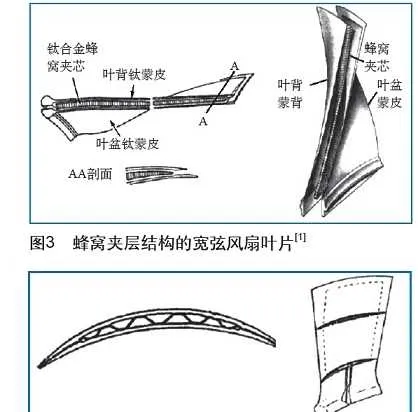
兩種結構的空心風扇葉片(李惠蓮, et al. "大涵道比寬弦風扇葉片連線結構設計及分析研究." 航空科學技術 5 (2011): 33-36.)
透過在葉片兩層鈦合金之間夾一層蜂窩狀結構或桁架結構,同時滿足了強度和重量的需求。此外,風扇葉尖的速度已超過了音速,為了提高葉片的效能和加大風扇與壓氣機的喘振裕度,業界還對風扇的形狀進行了改進,設計了如第一張圖 GP7000那樣形狀異常復雜的 掠形葉片。 降低了氣流相對速度,提高風扇效率和流量。掠形葉片使風扇葉片效率進一步提高了3%~5%,空氣流量增加3%~10%。
大家都知道,鈦合金在常溫下強度高,塑性差。現在, 一片風扇葉片的長度已經長約1.5m 。 要用傳統工藝把鈦合金加工成這樣形狀復雜的空心結構簡直是喪心病狂! 所以,RR采用了超塑成形/擴散連線(SPF/DB)工藝,把鈦合金加熱到同步滿足鈦合金超塑性和可以進行擴散連線的溫度區間(好像是900℃以上), 一次性完成三層夾心結構的擴散焊接和塑性加工過程,制備出形狀復雜的空心風扇葉片。 這種工藝是非常了不起的,不僅制備出形狀復雜的空心鈦合金葉片,還大幅提高了效率。為了進一步減重和提升強度,最新的葉片已經是表麵包覆鈦合金的復合材料了。
GE90-115B最大推力約56.9噸,大部份推力(比例記不清了,好像80%以上,有誰知道麻煩跟我說一下)由22片風扇葉片產生,平均每片葉片至少產生了2噸以上的推力!(一輛邁騰才1.5噸啊。)
===============================================
航發和燃氣輪機的做功過程是布雷頓迴圈,如下圖。
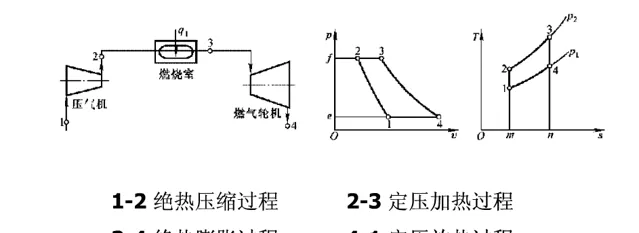
渦輪機做功的 布雷頓迴圈過程 。
布雷頓迴圈由壓氣機中的等熵壓縮、燃燒器的等壓加熱、透平的等熵膨脹和通向大氣的等壓排熱四個過程組成的理想熱力迴圈。其中壓氣機是完成這個迴圈最開始的步驟,簡單的說就是把空氣壓縮到20~50個大氣壓,為燃燒室中的等壓加熱過程做提供壓縮工質。
壓氣機是航發的核心部件。為了燃燒室中定壓加熱過程的穩定進行,壓氣機要在各種復雜環境下提供穩定的壓縮氣流。避免因氣流不穩定造成燃燒不穩、喘振,甚至引起發動機鈦火。此外,在保證穩定工作的前提下,壓氣機要提供盡可能高的壓縮比,提高發動機的效能。
現在主流的壓氣機是軸流式壓氣機(相應的還有離心式),被套用於各種客機軍機的發動機。每級風扇的壓縮效果都不高,采用多級風扇協同作用,最終達到較高的壓縮比。
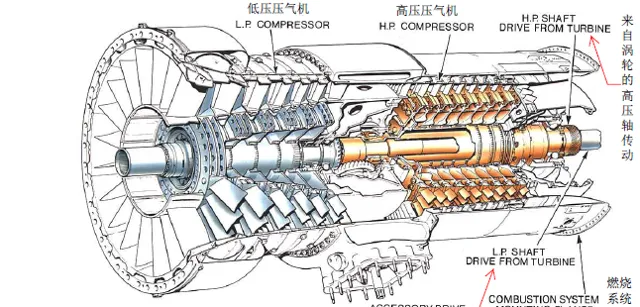
壓氣機采用轉子+靜子的結構,上圖中藍色和橙色部份分別為低壓壓氣機和高壓壓氣機的轉子部份。而它們邊上的白色部份為靜子。壓氣機中轉子透過旋轉壓縮氣流,靜子起到調整氣流的作用(後面再提)。
壓氣機的設計和制造涉及了眾多部門,這就是麻煩的開始——搞氣動的為了提高效率,增壓壓比,設計出他們的最優方案;搞結構的會發現,這種這結構在強度上不一定可行啊,回頭再修改設計再校核強度。多次返工之後,再給我們搞材料的,我們往往會發現,你們提的這些材料服役要求實在太苛刻的,沒辦法,只能重頭研發新材料,新工藝,要不就是重新修改設計。等到新材料新工藝搞出來了,最後甩給搞制造的。他們會發現各種稀奇古怪的構件和復雜的加工方案,肯定又是一陣頭大。。。
為了提高效率,壓氣機的轉子的葉尖要盡可能貼近機匣而又要避免和機匣接觸。在後面的渦輪部份第一張圖中可以看到,壓氣機通常的工作溫度為室溫~6XX℃,轉速為10000~20000RPM。
剩下的等等啊。。
================================================
渦輪部份:
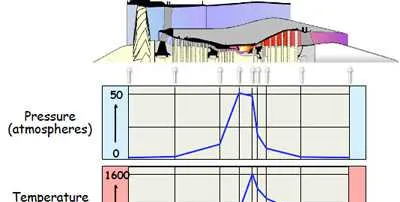
(來自Rolls-Royce)
大家最常聽到的就是航空發動機渦輪葉片相關的報道。如圖所示,航發裏面渦輪葉片是工作環境最惡劣的部件了。同時還要以10000~20000RPM轉速旋轉,承擔非常高的離心應力(密度8.x~9.x,比較重,銅的密度是8.9)。所以,最容易出問題(變形、斷裂、燒蝕、氧化等等)。我在北航陳光老師的【航空發動機結構設計分析】裏看到過: A380配的Trent 900發動機高壓渦輪葉片有70片,每片產生近600kW的功率。(邁騰1.8TSI發動機功率118k W,保時捷cayman2.5T發動機功率268kW,你們感受下航發的功率密度。 )
研究表明:燃氣進口溫度每提高55℃,在尺寸不變的情況下,推力提升10%! 為了提高熱效率,希望燃氣溫度盡可能高。所以導致渦輪葉片工作溫度能超過1600℃,已經遠高於葉片材料本身的承載溫度了(1000~1100℃)。
高溫下,材料在離心應力作用下會發生蠕變。簡單地說,材料發生蠕變的過程就像把一塊低溫下凍硬的橡皮泥加熱再用手拉它,橡皮泥會慢慢邊長。這樣會使葉片伸長跟機匣摩擦,導致斷裂(傳說中的甩飛刀)。(材料還會在使用中發生疲勞,可能導致疲勞斷裂,也會危及安全。疲勞牽涉到整機設計問題,而且疲勞比蠕變更復雜。)
為了能在這麽高溫的溫度下穩定工作現在,渦輪葉片一般采用鎳基高溫合金制造。因為鎳基高溫合金的蠕變抗力最好。另一方面,鎳基合金還有一些有利於高溫蠕變抗性的顯微組織結構,高溫會導致這些顯微結構發生退化,影響效能,這個太專業了就不細說了。為了提升材料的蠕變抗力,人們又在合金裏面添加了大量元素。其中部份元素價格高昂,如錸(4.7W/kg)、釕(1.1W/kg)、鉭等。為了研發效能優異的單晶高溫合金,需要進行海量的設計和實驗以及幾十年的積累。
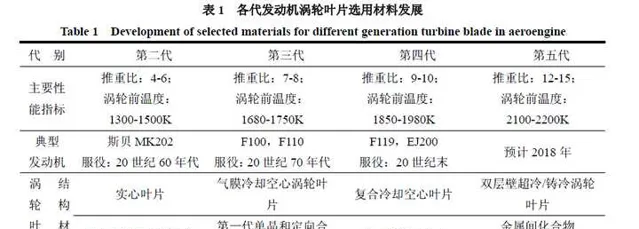
隨著航空發動機的發展,為了應對越來越高的渦輪前溫度,學術界和工業界合作,先後發展了多代高溫合金(董誌國, 王鳴, 李曉欣, 等. 航空發動機渦輪葉片材料的套用與發展[C]. 第十二屆中國高溫合金年會論文集, 2011.)
第二代鎳基單晶高溫合金被用在推比為9~10的先進航空發動機上(裝備台風戰機的EJ200和裝備F-22的F119)。
以第二代鎳基單晶高溫合金CSMX-4的成分為例:鉻6.5;鈷9.0;鉬0.6;鎢6.0;鉭6.5;錸3.0;鋁5.6;鈦1.0;鉿0.1,鎳61.8。每個元素都有重要的作用:有的元素能在高溫下提高蠕變抗力,有的穩定合金的顯微組織結構,有的提高抗氧化性(高溫燃氣會使金屬氧化腐蝕),有的可以提高承溫能力。可以看到,合金成分非常非常復雜,需要大量試驗才能找到最優或者接近最優的配比,達到最好的綜合效能。
此外,在自然冷卻情況下,合金都是由一個一個小顆粒組成的,那些小顆粒被稱為晶粒(晶體顆粒),晶粒之間的邊界叫晶界。晶界在高溫下是薄弱環節,所以先進航發都采用消除晶界的單晶葉片。也就是說整個葉片是一顆完整的晶粒,這就對冷卻和制造工藝提出了很高的要求。制造工藝圖就不發了,對大數人沒意義,其實網上也能找到示意圖。
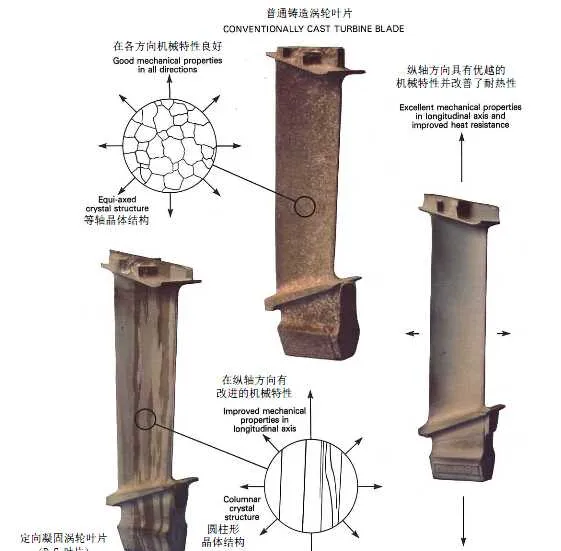
(來自Rolls-Royce)
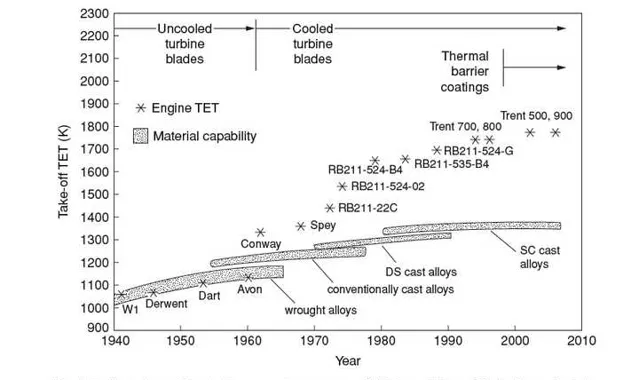
材料承載溫度的極限和在航發中使用溫度(渦輪前溫度)的缺口,就需要依靠先進冷卻技術來補足。圖右下部份SC cast alloys指的就是鑄造單晶合金,其左邊的DS是指定向凝固。看看材料的承載溫度,再看看航發的渦輪前溫度(trent800配屬B777,trent900配屬A380),是不是感覺很絕望呢 (Reed R C. The superalloys: fundamentals and applications[M]. Cambridge university press, 2008.)
當然,就算這樣,不考慮氧化燒蝕, 一個「裸」葉片的承載溫度最多也就1000℃上下, 為了達到1300~1700℃的承溫要求,還要在葉片內部設計制造非常復雜瓦斯冷卻通道和冷卻孔。把壓氣機裏面幾百度的「低溫瓦斯」從葉片內部引出來,從葉片表面的孔洞裏面噴出來,形成一道氣膜,隔絕高溫燃氣和相對低溫的葉片。這就是氣膜冷卻技術。發個空心葉片的演進的示意圖。大家註意,這個空心葉片是整體鑄造出來的,可以想象難度有多大。這個東西的外壁厚度是 0.5~1.x mm (可以想象制造的難度之高和承載的應力之大)。
隨著航空發動機渦輪前溫度的不斷提升,原有的單鍊結空心冷卻葉片的冷卻效果已經不能滿足需求,於是後來有發展了更先進更復雜的多通道多路冷卻方案。國外有人在搞雙層空心壁冷卻葉片,簡單的說就是雙層夾板加中空的結構,進一步提升冷卻效率。那就更復雜了。每一次冷卻方案的最佳化都對渦輪葉片的設計和制造提出了極大的考驗!
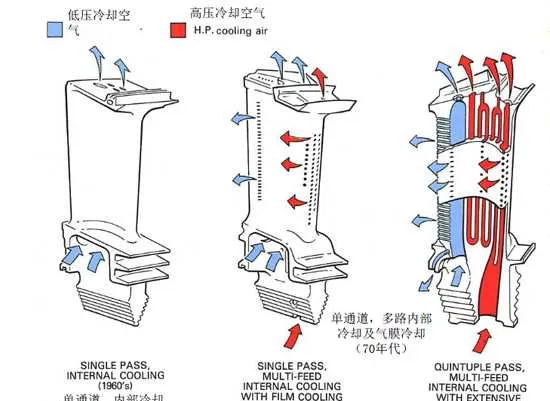
(來自Rolls-Royce)
==============================================
更新一部份關於空心渦輪葉片的內容。 國內最早做出空心渦輪葉片的是 師昌緒先生 的團隊。上世紀60年代,美國已經制造出了空心渦輪葉片。中國了解到國外已經開始采用空心渦輪葉片,要求科研機構研發自己的空心渦輪葉片。但是,當時完全沒有這方面的資料只能自己摸索。師先生的團隊後來探索出來的方法是往鑄件裏面放置石英管做型芯材料,最終解決了這個工程難題。 降低了葉片表面溫度約100℃ (每一代鎳基單晶高溫合金僅在前一代的基礎上,提高材料約30℃的承溫能力,100℃完全是重大突破)!使中國成為繼美國之後在世界上第二個采用鑄造空心渦輪葉片的國家!
==============================================
空心葉片在鑄造完成後還要進行電火花打孔或者雷射打孔,在葉片表面打出密集的冷氣孔洞。現在傾向於采用更先進的雷射打孔。這些孔洞的大小和排布都是精心設計的,能最大程度降低葉片表面溫度。
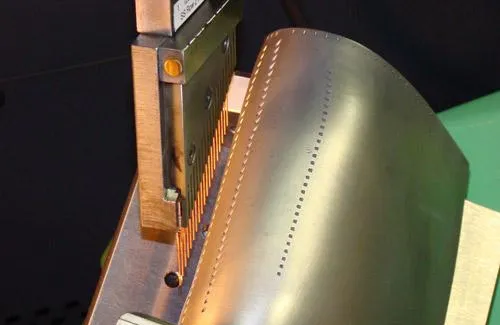
在鑄造好的葉片上打孔(侵刪)

空心葉片表面的冷卻孔(這張圖網上隨便找的。有個切開後能顯示內部結構的Al31圖片往這裏放不合適,湊合看吧,應該不難理解)
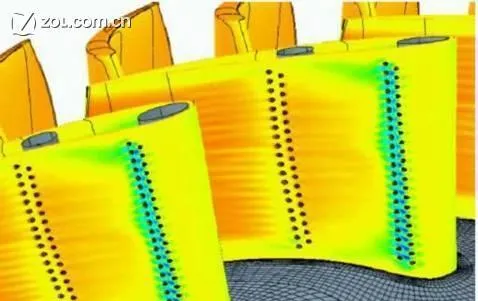
手頭沒有合適的圖片,從網上找了一張示意圖,幫助理解氣膜冷卻,侵刪。氣孔中的「低溫氣流」在葉片表面形成一層低溫膜,保護葉片。
然而,這還不夠填補材料承載溫度和使用溫度之間的缺口。在葉片上,還要再塗一層熱障塗層,繼續為合金遮蔽溫度過高的燃氣。 0.5mm左右的塗層能使葉片溫度降低100~2xx℃。 透過諸多領域專家學者的通力合作,才能使渦輪葉片在遠高於熔化溫度(熔化溫度是個範圍,~1400℃。合金在低於熔化溫度時就會軟化,無法使用。一般最多能在0.8~0.85Tm使用,Tm為熔點)下穩定使用,這簡直就是一件工程奇跡。
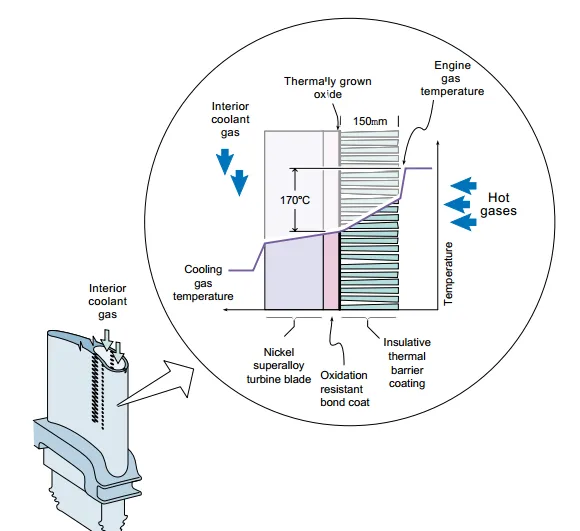
150微米(頭發直徑約80~100微米)的TBC(Thermal Barrier Coating, 熱障塗層)使葉片表面溫度降低170℃( Karaoglanli A C, Ogawa K, Turk A, et al. Thermal shock and cycling behavior of thermal barrier coatings (TBCs) used in gas turbines[J]. Progress in Gas Turbine Performance, 2014: 978-953. )
我只看過少量TBC的資料,盡我所能大概講講。完整的TBC系統一般是由金屬基體層、抗氧化連線層(TGO)和ZrO2加少量起穩定作用的Y2O3的陶瓷層組成。由於是把塗層塗覆在金屬基體上,需要考慮塗層的 附著力 , 對金屬基體顯微組織穩定性的影響 以及 塗層與金屬因熱膨脹系數差異而可能導致的剝落問題等等。這已經是葉片金屬材料之外的另一個學科領域了。
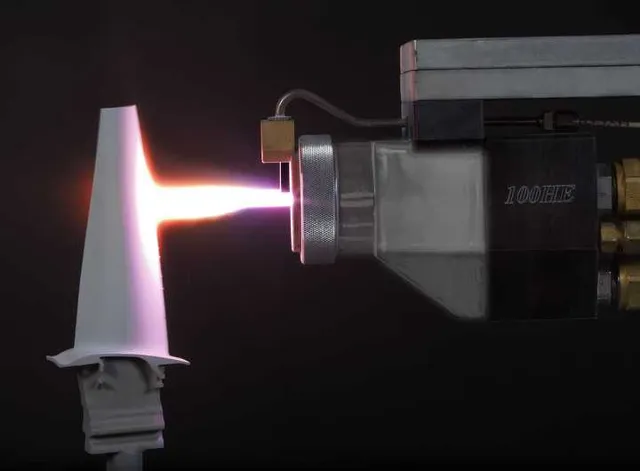
給葉片塗塗層(
Progressive Surface systems for shot peening, grit blasting, waterjet stripping, thermal spray, 2014)
在本世紀初,說一個單晶葉片的價格超過同重量的黃金是不誇張的。根據不同情況,軍用航發可能2~3級渦輪(F110:1+2,F119:1+1);民航更多(trent 900: 1+1+5,GE90:2+6),一個渦輪要裝一整圈葉片(註意:這裏說的主要是前面一級的高壓渦輪葉片。後面低壓渦輪葉片對材料效能的需求會有所降低,相對成本能降很多,要不然航發的價格還要高得多),大家可以算筆賬。而且,這個寶貝的成品率還特別低。
僅僅一個渦輪葉片就如此復雜,要求如此之高。先進航發還有壓氣機、燃燒室、排氣系統、傳動系統、燃油系統、控制系統等等不同的子系統。發動機對部件的加工精度要求極高,每一子系統的設計和制造都能把一個強國擋在大門外。而把各個子系統整合起來就又是一個大學問了。
大家公認德國和日本科技工業發達,但是在先進航發(尤其是先進大推力民用、軍用航發)方面,他們都沒有什麽讓人印象深刻的成就。這也就是五大國有資格玩、能玩得起的玩具。
先就這樣吧,困了,寫不動了。
=====================================================
我對上面部份答主的回答有不同看法,想討論一下。
=====================================================
@玉樹擋風給的圖片是壓氣機和風扇,其實它們承載的溫度並不高。當然,對設計和制造的要求一點也不低
-------------------------------------------------
@飛翔KIWI太專業的就不討論了,也沒人感興趣。首先,先進航發的渦輪葉片(之前的表述不準確,感謝評論中@夏天 知友的提醒)基本排除鐵了(機匣和傳動軸和渦輪盤會用到),基本全是鎳基合金(高壓渦輪葉片主要為單晶,中/低壓渦輪葉片可采用定向凝固和多晶合金)。鐵基合金高溫下組織不夠穩定,抗氧化性較差,高溫強度不足,這限制了套用。一般600~800℃使用。
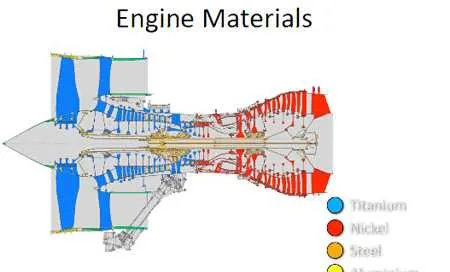
(來自Rolls-Royce)
軍用渦扇(戰鬥機)涵道比較小,更接近渦噴;為了追求效能和減重簡化結構,渦輪部份往往是1級高壓加1~2級低壓渦輪,導致尾部噴出瓦斯的溫度較高。
對於GE-90這樣的商用大涵道比渦扇,燃油效率是非常重要的指標。它主要由最前面的風扇向後推動空氣產生推力,核心機排出燃氣產生推力其實很少。燃氣主要作用是推動渦輪,帶動風扇;並不是排出燃氣越高,推力越大。商用渦扇可能是trent 900: 1+1+5,GE90:2+6的配置,透過高低壓渦輪層層吸收燃氣能量,降低最終排氣的溫度,使燃油燃燒釋放的能量更多的被轉化為發動機推力。經
@畢伍榮建議,再加一句「降低排氣溫度和速度以減少損失,民用大涵道比發動機是增加涵道比,增加渦輪提取的功,以分給更多的工質」