本文分享自華為雲社群【【雲駐共創】Huawei Mate 40產線直擊之華為雲IoT智慧制造助力工廠數位化轉型】,原文作者:啟明。
Part 1:智慧化工業4.0時代的數位孿生
一、工業0,智慧化時代已來
回顧人類歷史,我們共同順利經歷了三次工業革命:
第一次是蒸汽機時代,開創了以機器代替手工勞動的時代;第二次是電氣時代,自然科學的發展和工業緊密結合,科學在推動生產力方面發揮了更為重要的作用;第三次是資訊化時代,科學技術轉化為直接生產力的速度急速加快。
而今,我們迎來了第四次革命,即,工業4.0:智慧化時代。「工業4.0的本質,就是透過數據流動自動化技術,從規模經濟轉向範圍經濟,以同質化規模化的成本,構建出異質化客製化的產業。對於產業結構改革,這是至關重要的作用。」
作為新一輪的工業革命,工業4.0的核心特征是互聯。 工業4.0代表了「互聯網+制造業」的智慧生產,孕育大量的新型商業模式,真正能夠助力實作「C2B2C」的商業模式。
二、當前工廠數位化轉型痛難點
當前,大家都還在「工業4.0」的摸索階段。大量的工廠已經開始自己的智慧化轉型之路,比如透過構建套用來講采集的數據視覺化,講數據價值最大化。但是,在這個實踐過程中,問題不斷湧現,諸如:
1. 數據/資訊孤島,煙囪林立
一家工廠,在不同的階段,因為計畫的不同,有可能找不同的供應商去承接。分段式的計畫供應商,導致的是不同的系統套用。形象點說,多系統不互通,就是像獨立的「煙囪」,每個「煙囪」都有「煙」,但是卻不互通。在工業4.0階段, 不互通,意味著資訊孤島,也就意味著企業的數位資產分布零散,維護成本高,使用效率低下 ;
2. 套用上線慢,耗時耗力
正如第一點所說,不同系統之間的不互通,導致的是新的套用上線會「重復造輪子」:每個套用上線,都有大量的重復工作,浪費人力物力,且耗時長。更重要的是,新的套用帶來的數據處理問題:由於缺乏統一的建模,每個套用在處理原始數據時,都需要重復處理。兩個「重復」讓本就高昂的成本,更加「雪上加霜」;
3.數據分析門檻高
工廠,或者企業,有著一顆想要降本增效的心,比如想要透過分析現有的數據找到規律,從而最佳化流程,但卻因為數據分析的門檻高,望而卻步。這其中最關鍵的原因,是其業務場景不明確,沒有找到一個好的數據平台。
三、找對平台,是成功的一半
以上痛點難點,是大部份工業領域的廠家在「工業4.0」摸索過程中都會遇到的,而貫穿其中的是「套用」。也就是說, 軟體開發者未做到足夠的分層解耦是造成上述問題的重要原因之一 。以「套用」為基礎,工廠經歷了三個時期的三種模式:
1. 模式一:「煙囪式」套用
在工業4.0之前,由於缺乏套用和實踐,大部份廠家的套用,如上所述,都是「煙囪式」的:
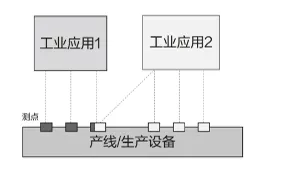
這樣便導致,一是缺乏整體規劃,各套用獨立部署,數據各自基於業務需要單獨進行采集和使用;二是效率低下,比如重復采集數據,對生產有較大影響。
2. 模式二:平台解耦——統一數采平台
在「平台」概念提出之後,工廠管理者們逐漸意識到,或許,在生產線和套用之間,需要有一個「平台」,這樣的解耦,能讓套用和生產線,套用和套用之間互聯互通。而這,就是工業4.0的一個基礎模型。
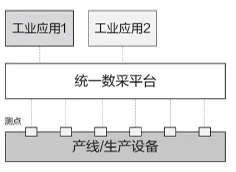
模式二的產生,讓專業的數據采集團隊完成盡可能多的數據采集,聯集中統一開放,讓整體效率有所提升。但是我們可以發現,即便是這樣, 數據的使用仍然是獨立的,沒有實作真正的融合。 在產線或者生產裝置取得的數據,仍然是後設資料,套用在取得數據之後,仍然需要單獨對數據進行二次加工處理使用,進而導致套用間對數據的處理仍然存在大量重復工作。
3. 模式三:數據處理——統一孿生模型
如何同步解決「套用解耦」和「數據統一處理」問題,華為IoT有自己的方法。
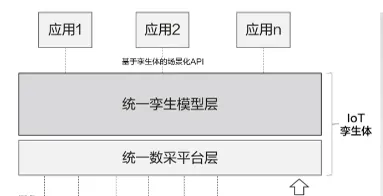
在物聯網領域,有「孿生體」這樣一個概念。透過「孿生體」把裝置的感知和裝置的認知,進行統一的處理。同樣以工廠為例,工廠裏面是有非常多的生產裝備、生產產線以及其他各式各樣的物理裝置的,那我們能不能幫助工廠把所有的這些物理裝置,透過統一的建模,對這些裝置一一進行處理,抽象為數位化的形象呢?
答案是,可以。透過把物理物件一一進行數位化處理,那麽套用和物理裝置的互動,就轉變成了套用和數位孿生體的互動。相對於前兩種模式,這種模式的開發方式有了一個非常大的變化:我們可以無視最底層的物理裝置,或者物理介面,將數據建模部份的工作,交由IoT的「統一孿生模型層」完成。
「孿生」這一概念,意味著我們在建模的時候,首先需要對模型有清晰的認知,也即廣泛的數采能力,畢竟在工廠裏面,會有各式各樣的裝置,這些裝置同時又有各式各樣的一些協定;其次,需要有非常高的抽象能力,你需要將物理世界的裝置,抽象成數位世界裏的模型,並且能進行互動。
數采能力和抽象能力,是目前開發物聯網套用過程中,非常關鍵的兩個能力。
基於華為雲IoT帶來新的開發模式,幫助使用者快速構建數位化轉型的基礎平台。
接下來以華為自己的工廠為例,來簡單說明華為雲IoT是如何使用新的開發模式,助力工廠數位化轉型的。
正如大家所知道的,華為本身也是一個制造型的工廠,華為雲IoT的能力首先是在自己的工廠進行實踐。我們以南方工廠,也就是Huawei Mate 40 生產工廠為例,把工廠的手機貼片過程透過數采、建模在數位世界中構建出一個數位化的產線的孿生體。
基於華為雲IoT的能力,在南向完成一個統一的孿生體,並在上層構建視覺化、智慧化的套用,具體架構圖見下:
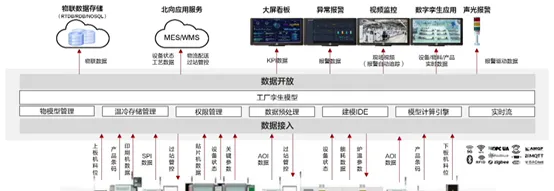
在南方工廠實際數位化行程中,有以下幾個挑戰:
那麽,如何站在開發者的角度,去省時省力地完成數位化呢?華為雲IoT正式登場。
四、以多維模型為核心,構建數位孿生
在一個數位孿生體的實際套用背後,是有很多的模型的,比如產線的模型,裝置的模型,品質缺陷的模型等等。而在建模過程中,從看待一個工廠物理世界當中的物理物件的角度,可以把工廠的孿生體分為兩類:制造的數位孿生和產品的數位孿生。
制造數位孿生 :
產品數位孿生:
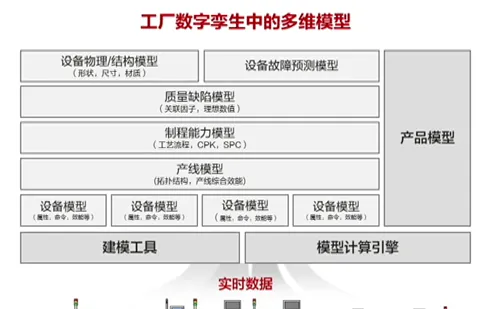
以上,就是工廠數位孿生的兩個非常重要的數位抽象維度。透過將產線生產過程透明化,實作生產有序可控,讓套用上線時間從原來的6-9個月,縮減至3個月;同時,孿生建模+智慧分析,用數據去驅動智慧生產,讓數據的開發效率能提升70%。透過華為雲IoT,我們可以 快速實作工廠的全要素聯結,並透過構建工廠數位孿生模型,大振幅提升數據利用效率 。
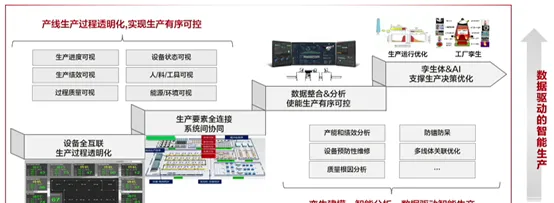
Part 2:基於南方工廠的數位孿生實踐
回到我們的主題。南方工廠,即是生產Huawei Mate 40的產線。手機產量的暴增,讓產線的數位化需求迫在眉睫。透過整個產線的數位化,可以提升生產過程、最佳化制造工程廠商的管理,以及品質控制的管理,讓產線的效率得到大大的提高,同時能夠降低營運的成本。
上圖是一個工廠孿生體的多維模型。我們可以看到在產品模型中,包括了裝置模型和產線模型,更上層還有制程能力模型、品質缺陷模型以及裝置物理/結構模型和裝置故障預測模型。
透過套用華為雲IoT數據分析服務建模和分析能力,可以快速構建的電子工程產線和裝置孿生體。那麽本文我們就來介紹一下如何構建一個數據分析服務建模。
一、基礎概念介紹
(一)OEE概念簡介
在進行建模講解之前,我們先普及一個基礎的概念。OEE,即裝置綜合效率(Overall Equipment Effectiveness)。一般來說,每一個生產裝置都有自己的理論產能,要實作這一理論產能必須保障沒有任何幹擾和品質損耗。OEE就是用來表現裝置是的生產能力相對於理論產能的比率。
在計算OEE的時候,會涉及到以3個維度:
那麽最終的計算公式就是,OEE=[時間利用率]*[效能利用率]*[合格率]*100%,這就是衡量裝置綜合營運效率的一個關鍵指標,也是很多電子制造工廠以及其他類似廠房裏的一個關鍵性指標。
一般來說,國內廠家OEE的數值都不會太高,一般只有70%,或者80%,少的甚至只有40%左右。
(二)工廠孿生體產線和裝置建模分析效果圖
工廠孿生體產線和裝置建模分析,可以透過一些視覺化的管理後台進行檢視。以下分別三個不同功能的效果圖。
Picture 1:圖上共有3條產線,可以進行適當地拖放。圖裏可以看到每個裝置的OEE數值。透過資產建模和分析能力可即時計算出產線和裝置的OEE,各裝置關鍵指標即時監控,同時可檢視歷史數據。
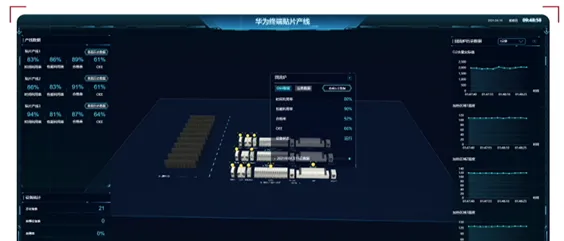
Picture 2:裝置建模圖。透過裝置上報故障訊息和裝置模型相結合,即時監控裝置執行狀態。

Picture 3:資產分析圖。透過資產模型分析能力,可實分時析和監控上報的裝置數據是否存在異常。比如說,濕度正常情況下是到45%~63%,如果上報的數據不在這個範圍內,則屬於不正常數據。界面就會顯示一個黃色的點,表示這裏的裝置上報的數據有異常。可以看出,數據分析是可以即時計算,即時監控的,如果有些嚴重異常的話,甚至可以推播到運維人員。
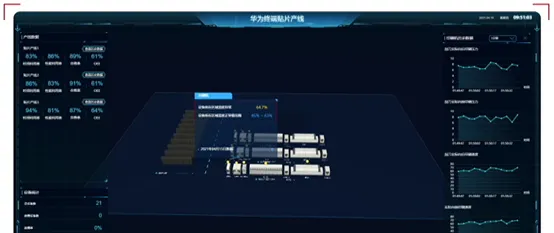
(三)工廠數位孿生Demo數據處理和分析流程
要實作上述的效果圖,我們需要經過如下幾個步驟(因為不是真實工廠,所以采取的是模擬裝置):

(四)IoT數據分析內的分析過程
接下來,我們來重點講解一下「IoT數據分析服務」內部的流轉過程。
第一步,數據管道。我們透過數據管道把數據接進來,同時本地也會進行備份;
第二步,對裝置進行建模;
第三步,建立裝置資產;
第四步,把模型例項化之後的裝置,及灌進來的數據,透過裝置資產分析這個計算引擎,完成即時計算相關的分析任務;
第五步,把數據儲存到IoT內部;
第六步,把這個數據透過API開放給第三方使用。
具體見下圖:

在這個過程中,我們需要詳細講解一下第二步以及第三步是如何操作的,也就是,我們如何建立模型和資產呢?
(五)IoT數位孿生的基本概念介紹
在進行建立模型和資產講解之前,我們先介紹一下「IoT數位孿生」的基本概念。
我們認為,物理世界的物,在數位世界中是有一個即時的、準確的一個對映的,它可以把實際的裝置數據和一些其他的數據組織起來,組成jason模型,成為一個載體。
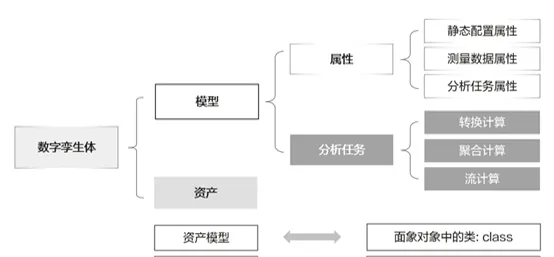
上圖是我們數位孿生的一個概念圖。
首先數據孿生體,可以分為模型和資產兩部份。其中模型相當於開發過程中,Java的類,表示一個類的一個樣版。在例項化之後生成一個資產,就相當於new class,那麽也就生成了一個物件。一個物件對應一個資產。
同時,模型又分為兩種,第一種是內容,內容還可以往下分還要分三種:
第一種是 靜態配置內容 ,此類內容不需要裝置上報,也不怎麽會有變化,比如產品型號,裝置型別等等;
第二種是 測量數據內容 ,測量數據內容是需要裝置上報的。通俗一點說,就是,數據分析自己是沒法得到的,需要別人給系統的數據。包括裝置上報的內容,也有可能包括從第三方的業務系統讀到的內容,系統都認為是一種測量內容;
第三種是 分析任務內容 ,此類內容在數據上報之後,是需要去進一步計算的。
針對最後一種任務分析內容,有相應的任務去配置,去計算。在這個過程中,相當於演算法的載入及配置:先去分析這個數據,然後後台的計算引擎就去載入配置的業務邏輯。分析任務內容目前有分三種:
第一種是轉換計算: 舉個簡單例子,假設建立的時候包含了兩個內容,a和b,而我們要求在這個過程中,a+b=c,那麽這就是一個轉化計算。轉化內容要求是即時的,且ab兩個值的數據時間戳是相同的;
第二種是聚合運算: 聚合是一個時間維度的計算,假設要求過去五分鐘的一個平均溫度,如果裝置每五秒鐘上報一次數據,那麽就需要對五分鐘內的所有上報的數據做一個平均,相當於在時間維度下,做聚合運算;
第三種是流計算: 流計算主要是用在比較復雜的場景,邏輯不能用簡單的一個if /else表達出來的時候,就需要使用到流計算。舉例來說,當資產將很多參數上報之後,系統需要透過這幾個參數計算出一個結果,再返回資產,那麽流計算在其中的作用就相當於一個小算盤。流計算的功能非常強大,在工廠數位化模型中,大部份的場景都能實作,比如滑動視窗、數據過濾、加內容等等,是比較通用的一個能力。
以上就是一個整體的建模的概念,基於上述的這些概念,我們能更好地理解後面的內容。
二、資產建模實操
(一)裝置建模:SMT產線印刷機裝置
對物理世界事物構建數位資產模型時,必須先定義好資產模型,然後再建立資產。一般來說,一個產線有7種裝置,我們以其中的印刷機為例,來講解一下裝置是如何建模的。
首先,是內容的配置。 針對於印刷機,我們三種內容分別為:
靜態配置內容:產品理想印刷時長、裝置型號
測量數據內容:印刷速度、脫模速度、印刷高度
分析任務內容:時間利用率、效能利用率、合格率、OEE
而分析任務內容同時又有以下計算配置:
轉換計算:計算時間利用率、計算效能利用率、計算OEE以及判斷溫度狀態
聚合計算:計算實際工作時長、計算實際工作時間、計算合格率
流計算:SMT場景暫未使用
下圖為內容編輯的頁面,包括靜態配置、測量數據以及分析任務,可供參考。
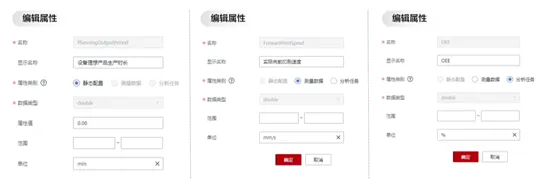
下圖為所有參數都配備完成之後的完整樣例。在這裏面可以看到大概有70個左右的內容,這些內容都是模擬了真實產業的一些內容。下圖所有的數據,包括樣本和格式都是來自於南方工廠實際的生產數據,所以是相對比較真實的。
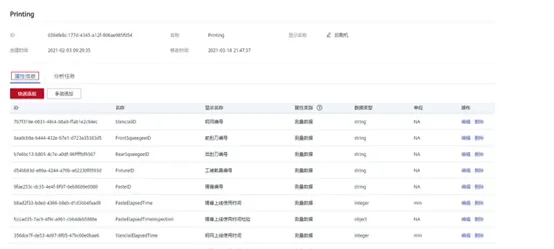
透過下面的截圖,我們希望能夠說明印刷機的 分析任務是怎麽配置的 。以「轉換計算」為例,只需要讀取上報的溫度值,並做一個運算式判斷,比如說溫度大於25,小於35,那麽就認為是正常溫度。把判斷的結果復制給套用,套用就能直接使用這個結果。
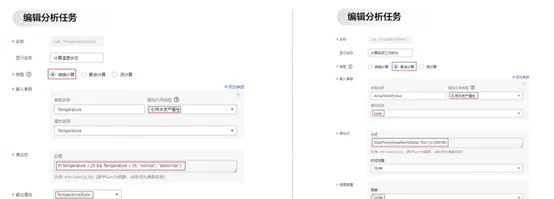
下圖為配置好的分析任務。可以看到,我們目前配置好了11個分析任務,包括計算資金利率、效能利用率、合格率、OEE、以及各種狀態的判斷等等前面所說過的種類。
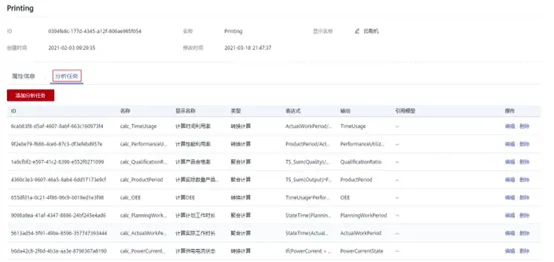
(二)產線建模:SMT產線
前面說完了「裝置建模」,接下來我們講解一下「產線建模」。
產線建模實際上也和裝置建模的概念相同,模型類似。但是靜態內容和測量數據內容暫時沒有配置,因為產線相對簡單一些,主要是求OEE的值,也就是分析任務內容,包括OEE相關的四個指標,以及轉換計算、聚合計算和流計算。
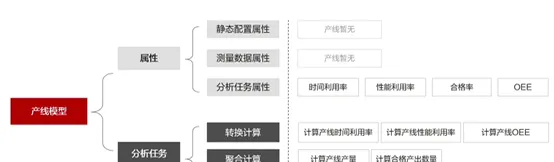
分析任務內容的配置和裝置產線是一致的,就不再重復講解。
下圖為印刷機的裝置資產配置圖範例:

接下來,我們來看看產線資產是如何構建的。如下圖,產線資產一共分三層:
第一層是工廠(父資產);
第二層是產線(子資產);
第三層是裝置(子資產)。
產線和裝置同樣有模型,三層模型構成了一個「父子關系」的資產數。資產來自於模型,由模型例項化而來,同時,模型例項化為資產時可以根據業務場景來指定層級關系,且資產之間相互獨立。
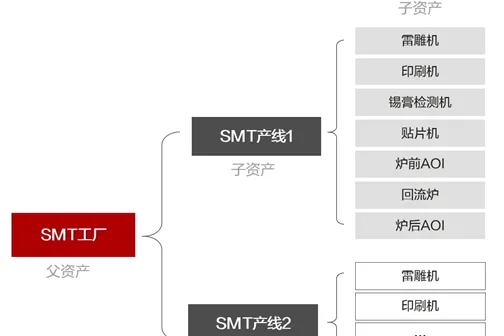
下圖是構建好的資產樹。相比於上一張圖的邏輯圖,這是一個範例圖。圖中表明一個電子工廠有三條SMT產線,每條產線有7個SMT裝置。

(三)、OEE相關指標配置(裝置&產線)
我們再來看看裝置的每個指標是如何計算的,如下圖。我們以「產品合格率」(下圖灰色部份)為例。
如前文所述,合格率=[合格產出數量]/[產出數量]*100%。表格中「TS_Sum」表示時序求和,即可以把產量在一個時間範圍內求和,比如,對五分鐘內的產量進行求和。其他指標的計算方式和合格率類似,就不一一贅述。
產線和裝置的指標計算過程相似,差別在於數據的來源。產線的數據來源於子資產,而非產線自己產生的。因為資產「父子之間」的數據是可以相互參照的,而產線本身是不上報任何數據的。
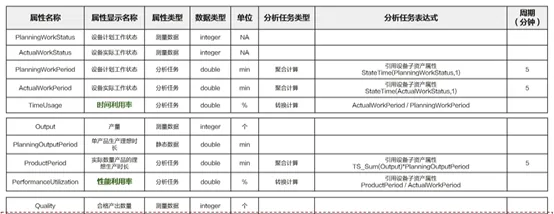
(四)資產執行監控
所有的產品建立、內容配置都完成之後,即可點選「釋出」,將模型釋出並執行。模型在定義的時候,本身是一個靜態的過程,一旦釋出,就會啟用。根據前序定義的任務分析邏輯,系統將會自動計算,並得出即時結果,進行上報。所有的數據都可以在下圖中觀察看到。
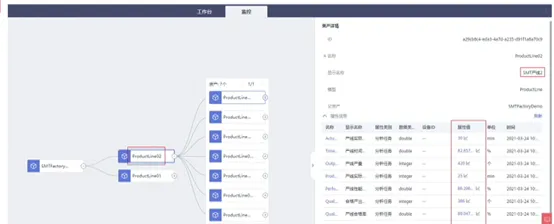
除了上述的數據展現模式,還可以根據業務的需要,將數據展示成折線圖、熱力圖、曲線圖等等,更易進行分析的圖形展示方式,得出你想要的結果。範例圖如下。
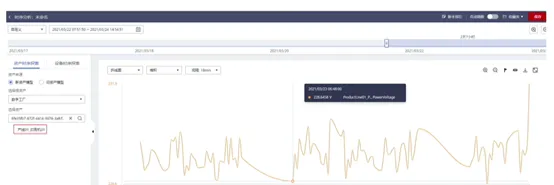
想要體驗一個產線模型建立的過程,可以前往華為雲IoT數據分析服務(https://www. huaweicloud.com/product /iotanalytics-platform.html )深度體驗。根據「總覽」頁的指導一步步進行操作。
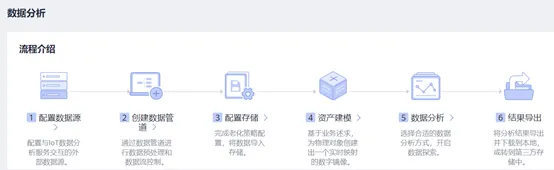
三、小結
從上述的講解和介紹,我們可以得出以下結論:
華為雲IoT數據分析服務基於物聯網資產模型,整合IoT數據整合、清洗、儲存、分析、視覺化,為IoT數據開發者提供一站式服務,降低開發門檻,縮短開發周期,快速實作IoT數據價值變現,讓工廠數位化轉型升級「觸手可及」。
來一起體驗一下吧~
點選關註,第一時間了解華為雲新鮮技術~