本文,主要参考【运动控制系统原理与应用】,【实用运动控制技术】,初步梳理一下运动控制的发展历程和关键的知识点与概念。
运动控制(motion control)是自动化控制的一个子学科。
一、运动控制系统的组成
一个运动控制系统,通常由驱动器、控制器、传感器三部分组成。
1.控制器:
常见的运动控制器主要有: PLC(可编程逻辑控制器) 、 独立式运动控制器 、 运动控制卡 、 专用运动控制器 等。
1) PLC
PLC主要功能是对开关量进行逻辑控制,并有简单的运动控制(直线轨迹控制)、运算数据处理等功能,通常采用触摸屏作人机界面。为扩充其应用领域,各厂家为客户提供了各种选配功能模块,如多轴运动控制模块、网络通信模块、模拟信号与数字信号转换模块等。PLC具有工作可靠、编程简单等优点,但其运动控制功能相对简单,若选用多轴运动控制模块,则价格较高。
2)独立式运动控制器
独立式运动控制器配有显示屏、按键和功能完善的控制指令,并有各种通信接口,控制电动机运动的能力比PLC强大。可完成直线插补、圆弧插补、轨迹控制等功能,且编程简单。目前,国外的运动控制器都具有现场总线控制功能。
3)PCI总线型运动控制卡
由于PC机运算速度快、存储量大,而且Windows操作系统的软件资源丰富,采用VB、VC等软件编写用户程序,功能十分强大。很多自动化设备都离不开PC机,特别是采用机器视觉检测的自动化设备、需要运行AuoCAD等大型软件的设备和需要采集存储生产数据的设备等,因此,这些设备采用 基于PC机的PCI总线型运动控制卡 与 PC机 一起组成运动控制器。在所有的运动控制器中,运动控制卡的功能最强,但其工作的稳定性可靠性较差。
4)专用运动控制器
专用运动控制器是针对特定的设备专门设计的运动控制器,如绣花机控制器、缝纫机控制器喷绘机控制器等。专用运动控制器通常以 单片机、ARM等芯片 为核心设计,其集成度高、价格便宜、使用方便,软件是为专用设备特殊设计的,客户可直接使用。其硬件、软件的设计都充分考虑了专用设备的工艺要求。
相对于专用运动控制器而言,PLC、独立式运动控制器、运动控制卡被称为通用运动控制器。
2.驱动器:
作为运动控制中的执行部件一般有电动式、 液压式及气动式三类。
电动式执行部件动作灵敏,性能优良,控制方便,且容易小型化,已经得到广泛的应用。运动控制中最常用的伺服电机类型有:直流(DC)伺服电机、无刷直流伺服电机、交流(AC)伺服电机和步进电机。按执行电机功率的不同,伺服电机可分为:小功率随动系统(100W以下)、中功率随动系统(100~ -500 W)和大功率随动系统(500W以上)。
每种电机都有相应的特点和驱动方式,详见裕如:机器人常用电机介绍
3.传感器:
编码器、力传感器、压力传感器等
二、运动控制系统的分类
1.按结构分类:
1)集中式控制系统
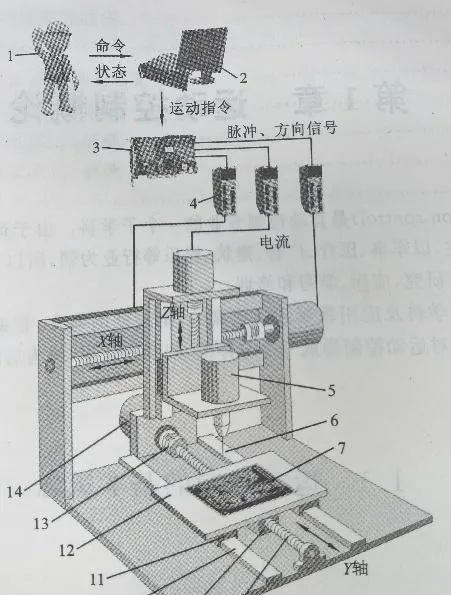
X、Y、Z三轴的伺服电动机由运动控制卡及电动机驱动器控制。运动控制卡内置于工业控制器(motion controller)。 操作员将电路板的设计图文件输人计算机,可得到电路板上各孔位的坐标数据。运动控制器的应用软件使用路径规划模块自动生成运动距离最短的钻孔路径。
根据此钻孔路径,应用软件调用一系列运动指令让运动控制卡产生相应的脉冲信号和方向信号控制伺服电动机驱动器,驱动器产生相应的电流驱动伺服电动机旋转,丝杠推动平台运动,使XY轴协调运动至各个孔的坐标位置,然后Z轴控制钻头完成钻孔动作。电路板自动钻孔机和手工钻孔相比较:X、Y轴平台运或代替了工人的左手调整电路板位置的动作;Z轴平台运动代替了工人右手操作机器使钻头上下运动的动作;运动控制器代替了工人的大脑控制整个钻孔过程。而且,自动钻孔设备动轨迹钻孔速度可达 300孔/分钟以上,钻孔精度可达士0.030 mm。
2)分布式控制系统
分布控制系统的特点是集中管理,分散控制,故也称为集散控制系统。它般分为三层:工作站层、控制层、设备层。
工作站层的作用是监督管理控制层负责完成系统的基本控制功能。分散控制使得系统的可靠性提高,局部的故障不会对整个系统造成重大损失。
由于分布控制系统为多级主从结构,低层单元之间进行信息交流必须经过主机,从而使主机负担过重,效率较低。一旦主机发生故障, 整个系统就会瘫痪。分布控制系统的通信多基于串行通信接口,速度较慢,而且通信协议较封闭,这极大地约束了系统的集成和应用。
3)现场总线控制系统
基于以太网的现场总线控制系统
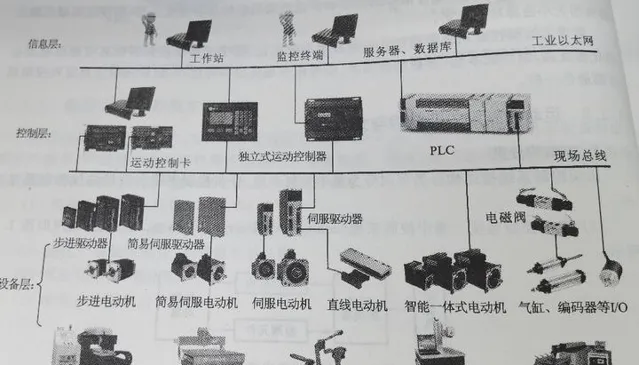
2.按处理器芯片分:
1) 基于计算机标准总线运动控制器
它利用计算机硬件和独立于计算机的运控控制板卡相结合而构成,与编程人员编写的控制程序相配合,使其具备高速的数据处理特性。运动控制板卡与计算机的总线连接形式有 PCI、PCI-E、并口、RS232 接口和 USB 接口。运动控制器主要使 用 DSP 或者 FPGA 等专用芯片,主要控制程序如轨迹规划、高速插补、伺服控制专 用 I/O 等主要都运行在专用芯片上。通常使用者可以根据其开放的函数库,在 Windows 和 Linux 等平台下自行开发应用软件。
2) 软开放式运动控制器
软开放式运动控制器是基于 PC 的运动控制,其所有的运动控制软件都安装在 PC 上,其硬件部分包括上位机 PC 和下位机负责具体发送与接收控制指令的外部 I/O。在操作系统平台,开发者在实时核内,开发运动控制模块,可操作性和灵活性大大增加。由于使用的是大规模制造的 PC 降低了制造成本,基于操作系统开发的软件,改造和升级灵活,为发开人员提供了一个开放性的开发平台。
3) 嵌入式结构的运动控制器
这种嵌入式控制器的特点是把 PC 上运行的系统移植到了里面,各硬件专用性很强,它可以单独运行系统。这个运动控制器的特点是把 PC 嵌入到运动控制器中, 各硬件专用性很强,它可以独立运行。控制器与控制器之间可以通过总线方式进行 通讯,在工业自动化当中广泛应用。
3.按控制方式分类:
1)开环控制系统
类系统应用最广泛,为数字式运动控制系统,通常都采用步进电动机。操作者接通机器电源、按下自动加工按钮后,运动控制器根据自动加工程序向电动机驱动器发送指令脉冲P;驱动器采集指令脉冲的频率、脉冲数,并对控制信号进行功率放大,通过调节步进电动机线圈的电流i从而控制步进电动机的运动;步进电动机将电流信号转换为机械运动,输出相应的转速和转角a;传动机构将电动机输出的转角信号转换为运动平台的位移量x。

2)半闭环控制系统
这类系统也是数字式系统。这种系统中的电动机都配有旋转编码器,它将电动机输出的转速、转角信号反馈到电动机驱动器中,在电动机驱动器闭环控制下,可以确保电动机输出的转角位置十分精确。目前交流伺服电动机、直流伺服电动机,以及部分步进电动机都配有旋转编码器,其驱动器都具有位置闭环控制功能。
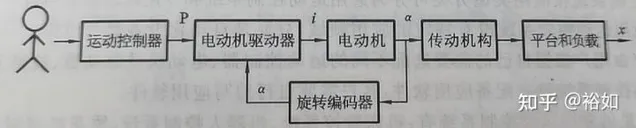
3)全闭环环控制系统
这种系统的运动平台上安装了光栅尺,用于检测平台的实际位置,并反馈给运动控制器。控制器根据反馈信号随时调整发给电动机驱动器的信号,使运动平台的误差始终控制在精度范围以内。
对于全闭环控制系统,其传动机构、运动平台和负载产生的各种误差都即时反馈到运动控制器中,并能立即得到补偿,所以该类系统具有控制精度高的特点。
全闭环控制系统多为模拟式系统,现在也有数字式闭环控制系统。
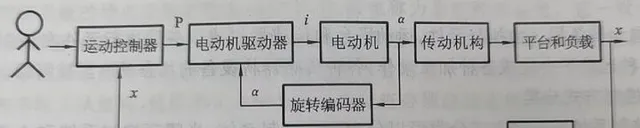
三、运动控制系统的案例——机械臂
作者:韩峰涛 链接:https:// zhuanlan.zhihu.com/p/28 052497来源:知乎 著作权归作者所有。商业转载请联系作者获得授权,非商业转载请注明出处。
我们使用类比的方式,参考计算机行业的分层形式来介绍机器人控制系统的范围,见下图:
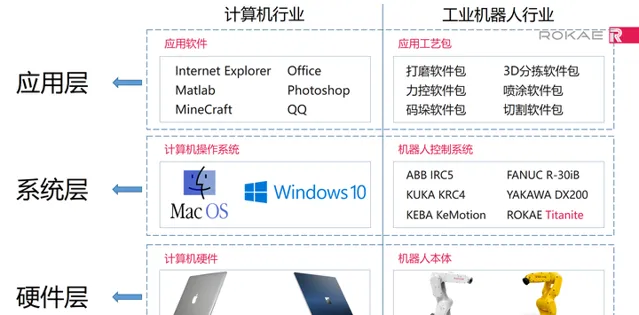
机器人的应用工艺包
如同计算机的操作系统一样,机器人控制系统在整个工业机器人产业中,扮演了最基础的软件平台的角色。
当你购买了一台工业机器人后,通过编程的调用其控制系统自带的基本功能可以满足很多场合的需求。如果自带的功能满足不了要求,那么可以
选装某些特定行业的应用软件包
,譬如打磨、力控、分拣、焊接、喷涂等。
控制系统提供平台,应用软件在平台的基础上扩展应用范围,提升使用体验。
在工业机器人发展的历史进程中,有很多优秀的细分应用软件公司,通过使用新的技术,研究新的工艺,在某个细分方向上成功拓展了机器人的应用范围。这些公司有的独立成长为了某个工艺领域的应用专家,利用与机器人厂家定制的专用机器人加自己独到的应用软件包在细分领域独领风骚,例如喷涂的DURR,焊接的CLOOS等;有的则成功被机器人整机厂商收购,其应用技术并入到机器人控制系统的框架中。
这几年深度学习技术在机器人路径规划、视觉方面有不少应用案例,这些技术增强了机器人在面对非结构化环境时的应用水平,同时也解决了之前通过固定编程方式不能解决的一些应用问题,对于扩展机器人的应用范围有着积极的意义。
那做机器人控制系统和做应用软件哪个难度更大,门槛更高? 这个问题没有绝对的答案,取决于做的深度与广度。微软也不敢说一定能做出媲美Photoshop的图像处理软件,Adobe全力投入几十年也未必做不出Windows,最终的答案取决于公司的发展历程与战略取舍,相信每一位深耕行业的专业人士对此都会有自己的判断。
机器人控制系统
Robot by definition is 「software-driven mechanical system「.类似于电脑和手机,工业机器人是一种非常典型的软硬结合、机电一体产品。
这样的产品都遵循这样一个原则:
硬件决定性能边界,软件发挥硬件性能并定义产品(机器人)的行为。在相对成熟的市场中,当大家使用的硬件趋于一致时,通过软件来进行产品差异化并创造价值是常见做法。工业机器人行业经过几十年的发展,硬件进步速度已经大为减缓,主流厂家的硬件配置基本相同,国产厂家也可以购买到与进口品牌相差不多的零配件(当前价格会高不少),这时机器人的控制系统就成为了决定机器人性能和功能的主要因素。
假如我们有两台机器人,配置分别如下:
- 进口ABB的机器人控制器 +国产伺服系统+国产减速器+国产机械本体;
- 国产机器人控制器 +进口伺服系统+进口减速器+进口机械本体;
那么哪一台的性能会更强,功能会更多?
答案想而易见,没有人会认为第二种配备国产控制器的机器人能PK过第一种使用ABB机器人控制器的机器人,即使性能好的方案除控制器外几乎全部使用了国产零部件。
既然控制系统如此重要,而且 到目前为止国内没有开发出可与市面主流机器人品牌原生系统性能接近的控制器产品 ,那为什么会有「控制系统门槛最低」的结论,或者说错觉?我觉得原因主要有三个:
- 国内缺乏对机器人控制和整机产品研发有深入认识的团队和公司 。对一个问题的正确判断有赖于对问题和背景的深入了解。国内工业机器人产业起步较晚,缺乏对高性能机器人产品研发有足够经验积累的团队和公司,误以为机器人只要能动起来那么控制系统就够用了,导致很多人错误的认为控制系统很简单。
- 国内机器人产品还普遍面向中低端市场,客户对国产机器人的性能几乎没有要求 。在这种市场需求下,很多公司对自己生产的机器人产品仅仅要求可以动起来,满足一些精度、速度、功能要求不高的场合,那么使用第三方的控制系统或者使用各种运动控制卡拼凑的控制器是可以满足要求的。我们不能说这样的做法是错误的,因为市场需求决定产品定位与设计,既然中国存在大量低端的需求,那么这样的机器人产品也就有其存在的价值。但是在相对有限市场空间的工业机器人领域,长期面向低端的公司将无法获得足够的利润来支持其走向中高端,如果国内所有的厂商都是如此,那么国产机器人行业将极有可能重蹈机床行业的覆辙,在短暂的销量高潮之后,跌落回出货量很大但是大部分利润被国外CNC软件系统商拿走的境地。
- 人们对于无法看到和无法直接对比的参数缺乏直观、准确的认识 。像减速器这种看得见摸得着的部件,有经验的老师傅可以非常直观的看出国产产品与进口产品之间有多大差距。大众更习惯于关注看的见的差距,而忽略真正隐藏在背后的差距。这种现象其实在计算机行业也有可参考的例子,各位现在可以回想一下自己平时用的生产力软件(Office、CAD、CAE、科学计算、仿真分析、视频剪辑、音频编辑、平面设计等),有多少是国内厂商提供的? 几乎没有 。国内正版用户每年都需要付出巨额费用来购买这些软件产品。但是在你的印象中,听到国内外CPU差距很大是多久之前?听到有人谈中外软件差距很大又是多久之前?抑或从来没有听过软件差距很大的说法?中外生产力软件产品之间的差距可能没有芯片之间大,但是仍然不能掩盖国产专业软件的落后,也正是这种思路的蔓延导致了机器人控制软件不受重视。
机器人的结构本体
从1973年ASEA(1988年,ASEA和BBC Brown Boveri合并组成了现在的ABB公司)发布全球第一台全电动工业机器人到现在已经过去了40多年,期间虽然减速器和伺服系统方面一直在持续不断的进行减少体积、提高响应性、降低传动误差等改进,但是这种改进更准确的讲是一种循序渐进的改良而非突破。工业机器人的应用领域能从最初的用来组装变速箱扩展到现在的焊接、喷涂、装配、贴片、点胶、打磨、抛光、分拣、搬运、码垛、检测、注塑、切割、测量、冲压、包装等数十个领域,绝大部分靠的是机器人控制系统在架构、控制、规划、工艺流程、人机交互等方面的革新。以最近非常火爆的协作机器人为例,虽然有着与传统机器人很大不同的外观,但仍应该将其看做是 在传统电机和减速器基础上的产品创新,或者更准确的说是控制的创新与软件的创新。
设想若干年后的机器人市场,彼时的赢家,靠的也不会是市面上花钱就能购买的所谓「核心零部件」,而是依靠掌握核心算法和完善功能的控制系统软件以及优秀的整机产品研发能力。因为机器人首先是「software-driven mechanical system」,是软件驱动的机电系统;作为系统整体而存在,也作为整体而设计。现实情况也正是如此: 主流的机器人都是自有控制系统 。硬件决定性能边界,软件发挥硬件性能并定义机器人的行为。任何一家想真正造机器人的厂家都不会放弃定义自家机器人行为的机会。