热管理架构在有了电动汽车的车型设计需求以后开始设计,主要功能包括: 1、冷却高压器件(电机、逆变器、车载充电机、DCDC);2、加热和冷却高压电池;3、加热和冷却驾驶舱。
明确了需求和边界条件才能开始确定热管理的架构,以下列举其中一些关键的需求和边界条件:
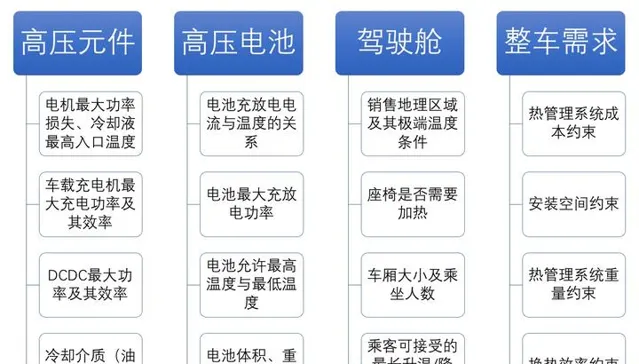
以上需求还只是冰山一角,但由以上需求可以基本确定热管理系统架构,再加上一些详细的需求参数可以对热管理执行器和传感器选型了。
下面就要开始做一些选择题了!
一、以何种介质换热?
换热根据介质的不同,可以设计出不同的架构。
五菱旗下的 宏光Mini EV 和宝骏E100 E200甚至E300使用的都是小功率电机,因此完全依赖 自然风冷 即可,而且除了电机以外的功率电子比如充电机和DCDC,也只需要外加一个 风扇主动风冷 散热即可满足需求,此时就没有水冷回路的存在了。
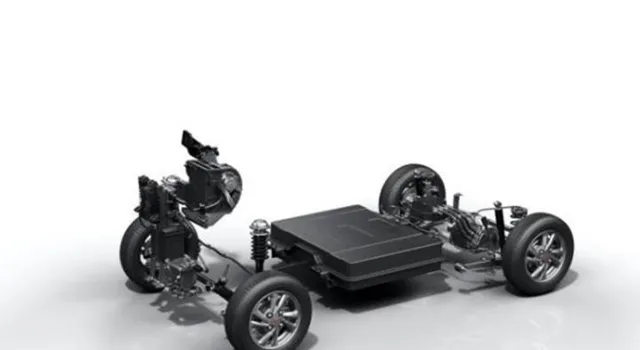
反之,而面向高端车型, 油冷 也逐渐被提上台面,主要是用在高端车型的油冷电机上,目的是为了拥有更高的电机转速/扭矩/功率,典型的是华为推出的 ePowertrain 的N合一动力总成集成,里面用的就是油冷电机。但是考虑到 油的黏度和成本 ,冷却油从电机内带走的热量并不是直接由传统的散热器和风扇总成来散走,而是要借助于 水油换热器 将热量传递给水路,然后又回到水路传统的散热方式实现散热。这也就意味着电机冷却有个自己的小循环。
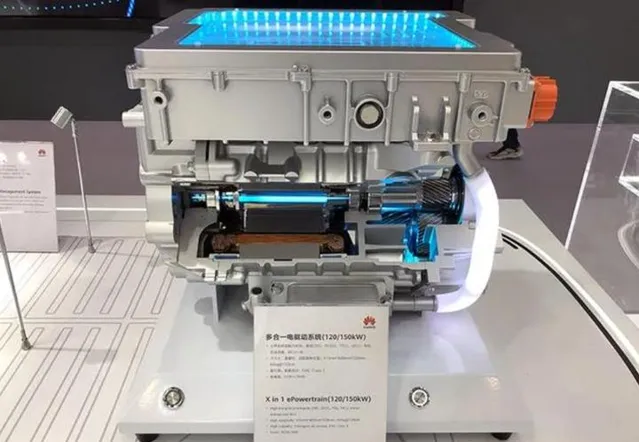
同样在电池处也有选择的机会,电池目前常见的是用普通的水路冷却,也有一些 直冷 方案是直接用制冷剂冷却,冷却速率更高,效果更好。还有的方案是使用特殊冷却液进行 沉浸式冷却 ,这种特殊冷却液为了能够更贴近电池单体模组,需要满足 非电解、绝缘、不腐蚀、低粘度 等等特殊的性质,如下图所示的3M电池冷却液。这些选择都是基于整车设计需求来的,比如说整车有个需求是电池要能够满足高功率直流充电,那冷却效果好的介质就很必要了。
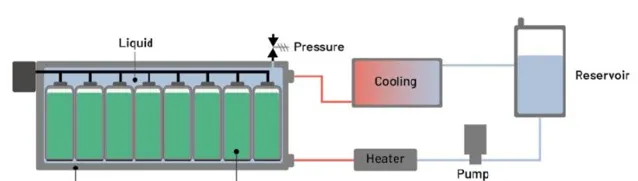
所以综合来看,换热介质主要有:空气、水和乙二醇混合液、制冷剂、冷却油、特殊冷却液。所谓热管理架构,也就是把不同介质的换热系统给搭建起来。
二、是否使用热泵系统?
热泵作为近几年热管理行业最火热的话题之一,很多造车新势力都计划在下一代车型中使用热泵系统,既有实际的节能效果,又可以作为卖点,毕竟作为标杆的 特斯拉Model Y 已经配上了。 蔚来 也在规划下一代使用 二氧化碳R744热泵 的纯电车型。
为什么是否搭载热泵系统对于热管理架构设计这么重要呢? 其原因主要在于,没有热泵系统的时候,电机、电池、乘员舱之间的热管理需求是由各自不同的系统满足的,互相之间至多只有一些串并联的结构,无本质区别(如下图中的菲亚特500纯电车型热管理架构)。而有了热泵系统,电机、电池、乘员舱的热管理变了一个有机的整体, 热泵成为了中间的重要枢纽 。
使用热泵系统的话,冷凝器和蒸发器就需要 根据热管理需求实现回路的切换 。传统空调系统中,冷凝器都是放在车前带个风扇散热用的,而在热泵系统里还需要考虑低温环境下利用冷凝器的热量加热乘员舱和电池,此时就需要有相应的回路将冷凝器的热量或蒸发器的冷量定向传递到所需位置。
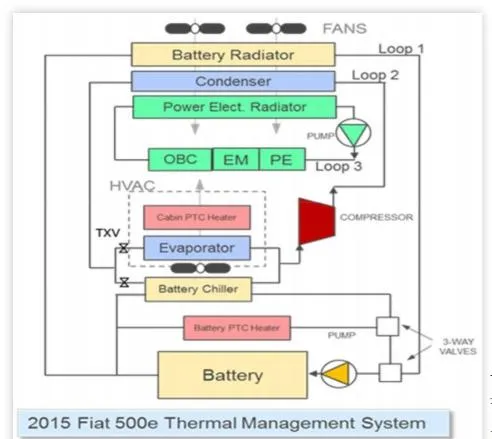
热泵系统的详细介绍会另外更新一章。
三、有没有可以整合的回路?
针对电机、电池和乘员舱的热管理需求设计好各自的热管理回路后,就要考虑如何集成在一起,因为回路集成和复用可以降低成本、减少空间。举例说明,磷酸铁锂电池耐高温但是低温性能不佳,三元锂电池低温比磷酸铁锂略强但是高温有过热的风险。因此针对中高端车型上的电池包,既有冬季加热也有夏季冷却的需求。而乘员舱正好也是需要 冬季加热夏季冷却 ,这两者的需求可以通过串联或者并联的回路设计耦合起来。
整合回路的需要做的是:1、减少 水泵 数量,但需提高水泵功率;2、减少 管路连接 ,但需增加 开关阀 切换回路,或者 比例调节阀 改变支路流量;3、减少 换热器 数量、但需同时兼顾回路中各个热管理对象的需求, 控制复杂度提高 。
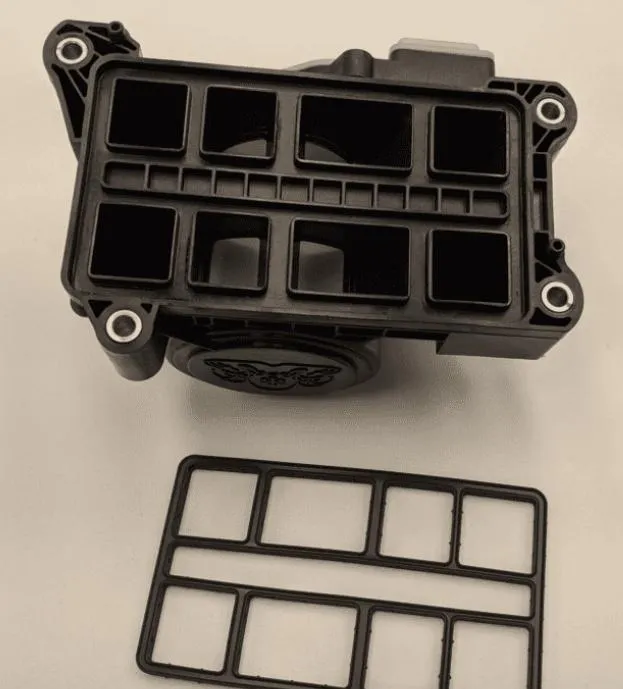
四、其它需要注意的点
热管理架构设计初稿完成后,就需要再做一些微调,有几个小点:
- 热管理回路中增设 传感器 --> 主要包括:电机入口的水温传感器,空调/热泵回路中的冷凝器和蒸发器处的制冷剂温度传感器或温度压力传感器,电池入口的水温传感器或电池模组的贴面温度传感器,冷却水回路的压差传感器(测流量/防泄漏),驾驶舱内的室温传感器,环境温度传感器(非动力总成范畴)
- 热管理回路中是否有可以 机械集成 的部件 --> 电子水泵和水阀是否集成,多个水阀是否集成(如上图中的特斯拉Model Y八通阀),水阀与温度传感器是否集成,电池包换热器与电池包是否集成,驾驶舱蒸发箱和电加热器是否集成,热泵系统是否集成(下图论文中的紧凑热泵解决方案)
- 热管理回路中在车上何处需要 弯折 、增设 补液壶 --> 为后期做 热管理仿真 做准备,因为管路的折弯处和补液壶的位置将影响管路内流体的流动阻力(流量)以及压力,对热管理仿真的换热效果有很大影响。
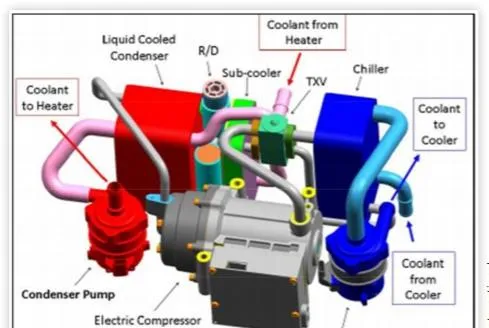
热管理架构设计尤其要考虑的是要避开现有专利 ,目前国内已有纯电动车型的热管理架构大同小异,架构设计简单但满足需求,但面向下一代车型的设计则需要在热管理架构上有一些创新,比如说:如何满足100kW以上的高功率直流充电冷却?如何通过热管理技术延长纯电续航里程?如何降低热管理系统成本以及提高空间利用率?如何做好100kWh锂电池的热管理?
期待更多在热管理架构上的创新设计!