文章來源:安世亞太官方訂閱號(搜尋:Peraglobal)
創成式設計是透過編寫演算法和程式來設計的過程,是一個人機互動、自我創新的過程,具體來說由設計師選擇生成模型的策略、編寫演算法,以人機互動的參數化建模,根據客觀的設計目標,結合仿真、最佳化方法,直到獲得最佳化的設計。安世亞太提出基於增材思維的先進設計與智能制造解決方案,利用創成式設計、拓撲最佳化、點陣結構設計等方法,獲得了很多先進設計經驗。
創成式設計能夠創造出手動建模所不易獲得的設計方案,它們擁有復雜幾何結構,而增材制造技術在工業制造中的套用優勢之一是制造復雜的結構,可以說創成式設計與增材制造技術是天生的「好夥伴」,創成式設計將進一步釋放增材制造的套用潛能。本案例,就以安世亞太利用創成式設計與增材制造結合,設計汽車輪轂的案例,體現了先進設計與增材制造技術的魅力。
增材制造為大規模個人化客製提供必要條件
在過去的100年裏發展起來的大規模生產滿足了大眾的各種基本需求。以汽車為例,大規模生產使得家家戶戶都能夠買得起車,汽車作為交通工具的基本功能得以實作。但是,除此之外,人們其實還有更高級的需求,如:對美的追求,希望與眾不同,彰顯個性。但在大規模生產條件下,這些需求被大大地壓縮,人們只能從有限的選項(如:幾種顏色、幾種材質、幾款樣式等)中去選擇,滿足個人化需求,對於大眾來說,幾乎是不可能的。基於傳統制造工藝和傳統設計方法的個人化客製就是「昂貴」的代名詞,它意味著要有設計師專門進行個人化設計,制造商要進行單件制造,而單件制造的費用可能與100件甚至1000件一樣,設計師的的設計費用更是可能高至天價。
現在,隨著增材制造技術和工藝的日益成熟,增材制造生產1000件不同的產品和生產1000件相同的產品,成本幾乎不會增加,這為大規模個人化客製的實作提供了必要條件。但還不夠,還缺乏一個充分條件——廉價高效的個人化設計 。傳統的基於設計師手繪式設計+手工CAD建模的設計方式設計的是單一模型,有多少個人化需求,設計師就得做多少個設計,這無論從設計師數量還是設計靈感上都是無法達到的。而創成式設計正是這種廉價高效的個人化設計的方法,它不再依賴手工建模建立單一模型,而是基於規則編寫演算法生成模型,一套規則可以生成無數種模型。設計師的任務已經變為建立規則,編寫設計程式了,生成模型的任務交給電腦自動完成。最終的個人化模型是由一組合適個人化的參數或條件來確定的。有了創成式設計加上增材制造工藝,就已經具備了大規模個人化客製的充要條件。
汽車輪轂創成式設計
汽車輪轂是最體現汽車個人化的部件之一,對輪轂的需求既有美觀,又有效能、輕量化、節能等各個方面。許多愛車的朋友購車後都會進行輪轂改裝,在改進效能的同時,彰顯自己的與眾不同。輪轂設計既有需要標準化的部份,也有可發揮創造力的造型設計,但是無論造型如何變化,滿足力學效能的設計目標不能變。
首先,標準化的輪輞部份,可以透過參照標準中提供的幾何關系建立編程規則,透過編程實作輪輞的參數化建模。
再來看輪輻的創成式設計,我們可以 透過定義幾何關系來確定模型生成規則 。如果我定義一種這樣的幾何關系:輪輻為成組的分支結構,分支節點位於一系列同心圓上,層間可以扭轉,分組數、分支層數、扭轉角、同心圓半徑分別為在一定範圍內可變的參數。那麽當我們改變任意參數的時候,就會生成不同的結果。假設分組數可取10個數值、分層數可取4個數值、扭轉角可取20個數值、同心圓半徑組合可取50種,扭轉範圍可取10種組合的話,那麽生成的結果將會有400,000種。這裏我們僅展示其中的幾十種。這裏描述的規則範例,只是一類規則,我們還可以建立其他形式的規則,以生成不同於分支結構的風格樣式。
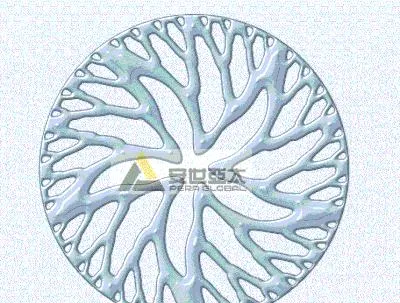
創成式設計非常靈活,根據輕量化目標,可以加入鏤空的結構元素。這些鏤空元素也是隨著輪輻形式以及輪轂規格的變化,按照規則自動生成的。
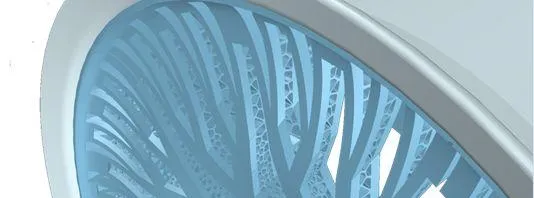
創成設計過程關註的是需求、功能、效能等需求,得到的結果無論多麽復雜,都可以透過增材制造制造出來,並且沒有增加成本。根據使用者的喜好,每一款輪轂的樣式都可以不同,無論小批次客製,還是大規模客製化,都不增加成本,這是增材制造的最大優勢之一。
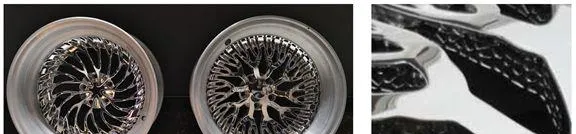
未來的個人化創成式設計可以是使用者參與的。設計師設計的不同類別風格的程式打包後發到互聯網上,開放一些參數給使用者,由使用者自主調節,即使用者參與的創成式設計,隨著使用者改變參數,結果千變萬化,選定樣式、材質等,完成線上客製下單。用一個公式描述就是: 創成式設計+增材制造=你參與設計+為你制造= 100%使用者滿意+ 尊享體驗。
該輪轂運用全新的創成式設計思維對輪轂進行設計。展示了創成式設計自然、生動、多變的設計優勢。為汽車個人化改裝客製提供了新的可能性。
如果您有其他的問題請關註安世亞太官方微信公眾號:Peraglobal進入安世亞太官方微信點選右下角提問區進行提問
或撥打客服電話:400-6600-388,安世亞太竭誠為您服務